Empowering Change
How a production site in Indonesia reinvented itself and successfully changed its safety culture along the way.
Even after almost 22 years, Ka Fung remembers all too well the day that changed his mind about personal safety. He had just started working at Clariant’s production site in Tangerang, about 25 kilometers west of Jakarta, Indonesia’s capital. He was hired as a maintenance engineer straight out of college. »It was my first job after leaving school and I was probably a bit too eager and carefree«, he admits. While working on the shop floor one day he stood up abruptly and banged his head on a metal rod. »I wasn’t wearing my helmet, and the hit nearly knocked me off my feet«, Ka Fung remembers. »I didn’t need stitches or anything, but it did bleed and certainly left a mark.« What Ka Fung realized then and there was how even small lapses might hurt you when you least expect it. »There wasn’t really anything that could have fallen on our heads at the time, so I felt no need to wear a helmet. But safety is never just about your own risk assessment in the moment or the dangers you can easily foresee«, he says.
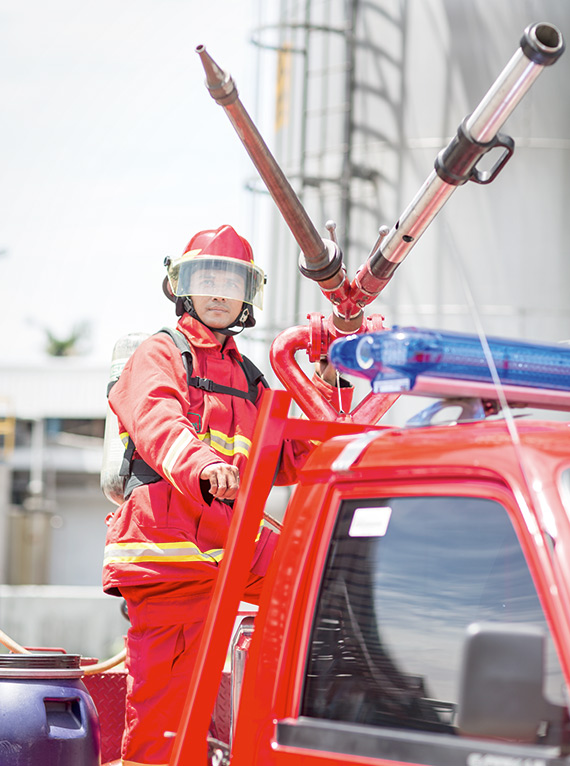
Weekly drills
To be prepared for any emergency the Tangerang site’s fire brigade performs weekly drills.
7
The last so-called Lost Time Accident (LTA) of a Clariant employee or a contractor at the Tangerang site happened seven years ago. A LTA is an accident on the job that results in an employee being absent from the workplace for at least one full workday.
Clariant’s site in Tangerang is special in several ways. It’s the company’s largest site in Indonesia and its headquarter in the country. In all, Clariant’s Business Units run six production sites and a couple of offices across three of the major islands, Java, Sumatra, and Kalimantan. Of the 700-plus people Clariant employs in Indonesia, more than a third work in Tangerang. Today, it is run as a multi-user site. That means it’s home to several Business Units of Clariant as well as other companies. The site and its main operation, however, are run by Clariant’s Industrial & Consumer Specialties Business Unit (ICS) which produces specialty chemicals and application solutions for consumer care and industrial markets. The active ingredients in conditioners are one example. Growing consumer markets in the emerging economies of Southeast Asia are driving demand. Indonesia is one such market. As the world’s most populous Muslim country, it drives trends in other ways too. It’s no coincidence that Tangerang specializes in products that rely on palm and coconut fat rather than tallow. The site recently received its halal certification under Islamic law, opening up a growing market of home and personal care products catering to devout Muslims.
Rewarding efforts
In 2017 Clariant Indonesia also received the Responsible Care™ Platinum Award honoring outstanding performance in terms of sustainable business practices. According to the auditors Clariant scored 98 out of 100 possible points, the highest rating among the more than 50 participating companies, most of which were multinationals. The Responsible Care™ Award is part of a 1985 charter by the global chemical industry promoting sustainable business practices. It is the first such platinum award given out in Indonesia in five years. Earlier in 2017 Clariant Indonesia received special recognition by Responsible Care™ Indonesia for outstanding performance in chemical transportation and distribution safety.
»Today’s setup of the Tangerang site is the result of major changes that began around 2012«, says Hans Herrel, the site manager and Head of Clariant’s operations in Indonesia. Before, Tangerang had been a production site mostly for textile chemicals and dyes. When Clariant sold parts of that business, some of the assets at Tangerang changed hands as well. »There was a lot of work to do«, Herrel remembers. »We had to physically untangle operations and the flows of materials. At the same time, Clariant wanted to establish Tangerang as a production site for ICS’s growing business in the region. So we had to redesign and partially rebuild the site.«
Literally moving facilities across the site, building new ones, de-coupling from sold-off assets and re-routing the flows of materials, utilities, products, energy, and waste — all this turned the construction efforts into a Herculean task. But Herrel, who has been with Clariant since the 1980s, took the shift as a challenge as well as an opportunity to improve. By 2015 Tangerang had seen not only the arrival of a new business but also the implementation of a state-of-the-art energy management system and new safety standards. »ICS actually brought a different class of chemicals to our site«, says Herrel. »Those came with higher levels of safety requirements, both in terms of equipment and organization.«
The construction work itself posed challenges of its own. »Having hundreds of third-party construction workers on site at a time is never ideal. That’s when we realized we had to improve our safety management«, Herrel says contritely. »We had no accidents during all this construction work but, in hindsight, we really missed the mark at times.« He chalks it up to a lack in safety culture both at the workplace and beyond. »If you’ve ever driven on the streets of Jakarta or elsewhere in Indonesia, you’ll notice that safety and traffic rules are neither followed nor enforced very strictly. That’s not to say that Indonesians are reckless. There’s just a very different attitude both towards risk and authority. You can’t just put rules in place and hope they’re followed. You have to actively change attitudes.«
Changing minds requires a lot of effort and understanding. Herrel knows a thing or two about that. He has spent most of his life working to improve and manage operations in Southeast Asia, be it in the Philippines, Singapore or Indonesia. In 1986 he was hired and trained explicitly to do just that. »Back then the company was desperately looking for engineers to improve operational standards at its sites outside of Europe«, Herrel says. As a student in Kaiserslautern he had spent his semester breaks working as a ski instructor and tour guide for American tourists. »So my English was pretty good, at least for a German engineer in the 1980s.« However, working with local teams and then trying to fundamentally change the way things are done is something he had to learn on the job.
4
Since 2016 on average 4 safety workshops have been held each month at the Tangerang site.
When it came to improving the processes and organization at the Tangerang site, Herrel was in his element. »Authority and strict rules only go so far«, he says. »You have to win people over. You have to show appreciation. And you have to give people ownership in a way.« A lot of the changes he and his local team implemented in Tangerang dealt less with technology than with attitudes. Or as he puts it: »The hardware was mostly in place. We had to update the software.« Safety concerns literally became item number one on the agenda of every team meeting. Herrel initiated what has come to be known as the »Clariant Tangerang Coffee Club«, a kind of regular powwow involving the entire staff of the site. Early, around seven thirty, more than 200 people gather in the lobby of the main building. »It’s a chance to mingle and to get updates on current developments«, Herrel says. »And we always start off with what’s going on safety-wise.«
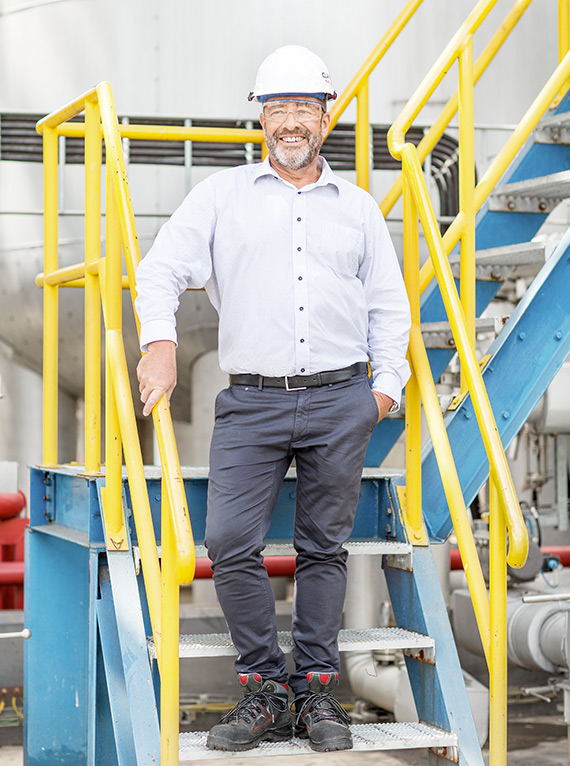
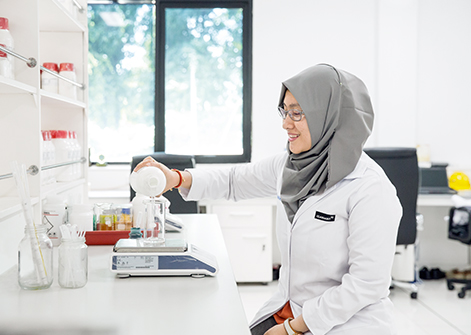
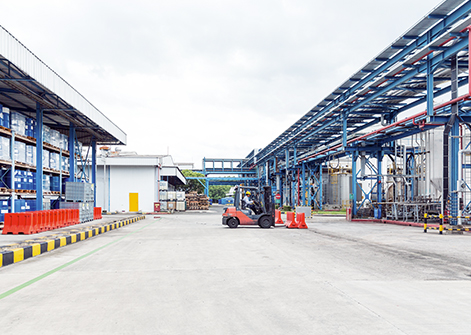
A new standard
Clariant's production site in Tangerang, Indonesia has been recognized for its outstanding performance in terms of sustainable business practices and safety.
»Safety is more than just putting rules in place. You have to actively change attitudes.«
Hans Herrel Country Head Indonesia
There has been no lack of topics for these meetings. Tangerang has seen hundreds of projects in environmental and work safety as well as audits by government officials, customers and Clariant itself. The company’s own excellence initiative kickstarted more than 250 projects to improve both efficiency and safety at the site. Safety workshops in 2016 and 2017 alone saw more than 1 200 participants. Herrel hired a retired military drill sergeant as the head of site safety and security. The site’s fire brigade was upgraded both in equipment and in training, and now performs weekly drills. Organizational changes brought further improvements. »We’ve fundamentally changed the way we oversee contractors working on our site«, says Ka Fung, who’s been involved in many of these changes. »What was once a centralized job is now being done at a more local level by the shop floor teams themselves. That means giving back ownership and responsibility to the teams and their supervisors for what goes on around them«, Ka Fung explains. »Once people feel accountable and in charge, they look out for each other more.«
2 439
In 2014 a global reporting system was put in place. Since then 2 439 near misses or potential accidents have been reported.
Reporting and reviewing so-called near misses is another essential part of this new awareness. In 2014 Tangerang put in place a system that lets employees document whenever they’ve witnessed a potential accident, an undetected hazard or risky behavior. So far almost 2 500 such cases have been reported. »This has nothing to with denunciation, but everything with learning from mistakes – both by individuals and the organization as a whole«, says Herrel. »Everybody makes mistakes. To learn from them is what counts. It helps us identify hazards we hadn’t foreseen, and it shows that we truly care about safety, not just about rules.« The message stuck early on, as Ka Fung remembers. From his early days as a maintenance engineer he has since moved on to become first a project engineer involved in the remodeling efforts on the site and eventually a so-called Lean Six Sigma Master Black Belt, which today sees him working to improve operational standards, processes and efficiency in Tangerang and beyond. It was his job, for example, to implement a state-of-the-art energy management system according to the ISO 50001 standards. At the time, Tangerang was one of the first three Clariant sites ever to do so – the only one outside Europe. »Before I got involved with improving standards and practices, I knew Hans only from my work as a spokesperson for the local union«, Ka Fung remembers. »Our exchanges on issues like pay or overtime were, let’s say, lively. But I soon also witnessed how engaged he was and how well he understood folks on the shop floor. I think that’s what made a big difference in the end.«
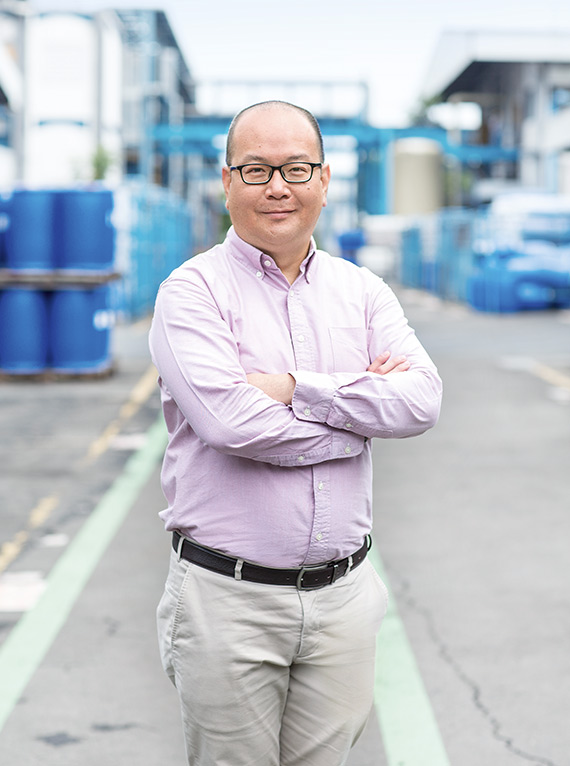
»Once people feel accountable and in charge, they look out for each other.«
Ka Fung Master Black Belt
The changes at Tangerang are evident, and they’ve drawn attention. In 2017 Tangerang was awarded the Phoenix Award, recognizing the site as the biggest improver in terms of safety across all of Clariant. As the name Phoenix suggests, the award honors improvement rather than absolute performance. In its valuation, the jury mentions specific changes as well as previous shortcomings. »We’ve come a long way«, says Herrel. His staff seems to agree. In 2017, Clariant was recognized as the region’s best employer in an independent survey by Aon, a consultancy. »But we’re also well aware that our work towards better safety and accident prevention is never done«, says Herrel. A sad reminder of this came in 2017, only a few months after the award for Tangerang, with a fatal accident at another site in Indonesia. An employee died after a stack of bulk containers collapsed on top of him. »The police have investigated the incident and found no wrongdoing. But it sadly shows that there’s never a time to relax in our efforts«, Herrel says.
There’s always a lot to learn and to improve. Tangerang may very well turn out as a model for other sites. As both Herrel and Ka Fung know, improving safety is about staying vigilant. It’s about dealing with risks both obvious and unforeseen. And it almost always starts with changing minds and getting new ideas into people’s heads. Preferably without bumping them.
A rating assesses the creditworthiness of a debtor. Ratings are mainly required for the issue of debt instruments and usually determine the level of necessary interest payments, among other things. Clariant currently uses the two rating agencies, Moody’s and Standard & Poor’s, for this purpose. VIEW ENTIRE GLOSSARY