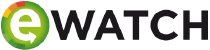
In the past years, Clariant has developed an extensive energy efficiency program under the name »eWATCH« which identifies savings potential through the calculation and analysis of energy consumption. This potential results from an optimized use of machines and systems. Machines are incorporated and used in the production process so that they run at or near the best level of efficiency. This is supplemented through a sharpening of the energy awareness of employees and through training in the areas surrounding energy-saving possibilities.
In addition, the management of energy supply and consumption is coordinated across the Group. A better coordination should on the one hand result in savings, and on the other hand, allow a better assessment of cost-benefit ratios from investments in savings, because an important additional condition of the investments required for energy savings is an amortization period of only a few years, generally three to five.
In the last ten years, Clariant has achieved impressive success with eWATCH. Through large projects, but also through many smaller projects, energy consumption per kilogram of manufactured products has decreased by more than 50%, or by 7.5% annually on average. The emission of CO2 and other greenhouse gases decreased to about the same extent. And despite higher production, even the absolute numbers for consumption and emissions fell. Energy consumption and CO2 emissions were in each case reduced by 4.5% per year on average, and thus by around 38% over ten years.
Clariant has already identified and achieved high savings potential. Now, additional savings will be attained by means of numerous small projects.
|
Investment costs |
Amortization period |
Savings (kWh/Y) |
|||
The fan upstream of a blow dryer could be switched off and bypassed when drying a newly introduced less dense product. |
EUR 1 000 |
0.5 Y |
18 000 |
|||
The output of an air blower was too high to accommodate lower loads. To supply low air flows, some air was bypassed and discharged. The purchase of a controlled smaller blower allows regulated air supply. |
EUR 22 000 |
1.2 Y |
143 000 |
|||
A heat-recovery system heats product tanks and piping. However, the recovery did not suffice, 9 000 tons of steam needed to be produced in addition. This is now eliminated with the use of an additional heat exchanger that recovers reactor off-heat (5 190 t of steam saved). |
EUR 5 000 |
<0.1 Y |
3 100 000 |
|||
The disposal of a bi-product from pilot reactors in a catalysis laboratory was significantly simplified using a catalytic post-combustion unit, saving energy and water. |
EUR 60 000 |
2.2 Y |
370 000 |
|||
The technical optimization of a steam generator with the incorporation of condensate recovery significantly reduced energy consumption. |
EUR 39 000 |
1.9 Y |
400 000 |
|||
The use of comprehensive LED lighting at the new location of the Biotechnology Group reduces day-to-day operating costs noticeably. |
EUR 45 000 |
0.8 Y |
191 000 |
|||
The renovation of the exterior lighting of a location with the replacement of the metal-halide bulbs with LED bulbs reduces energy consumption and maintenance, and allows for better illumination with an adjusted output. |
EUR 45 000 |
3.3 Y |
97 000 |
Investment costs include all expenditures that are allocated to the sustainability effect of a purchase. The amortization period gives the duration in years (Y) in which the reduced costs compensate for the investment costs. The savings indicate the reduction in energy consumption in kilowatt hours (kWh) per year (Y) made possible by the sustainability investment. The energy-saving measures initiated within the scope of eWATCH in 2015 will lead to an annual cost reduction of approximately CHF 6.3 million.
Employees’ ideas reduce costs and protect the environment
The experiences and knowledge of employees are a valuable source of ideas for continuous improvement of production processes. Clariant promotes the suggestion system at many locations and thus saves money year after year, for example, by reducing energy consumption or waste water pollution.
Through the optimization of the production process of pigments, effluents were able to be reduced by approximately 50% and waste water pollution (COD1) by approximately 20%. A team of employees of the departments involved in the production process developed the suggestion for the improvement together. Ideas were generated, assessed, and selected. The new production specification was then drawn up and implemented.
By changing the production process in the production of a pigment, the batch quantity was nearly doubled. Through the new process, the amount of liquids used in production have been cut in half, which leads to significant reductions in energy consumption. The result is a reduction of the steam consumption by 40% per kilogram of pigment and a reduction of the requirement for electricity and ice by 50% per kilogram of pigment.
1 The Chemical Oxygen Demand (COD) is as a summation parameter a measurement for the sum of all substances present in water and oxidizable under certain conditions.
Carbon Dioxide VIEW ENTIRE GLOSSARY
Pigments are substances used for coloring; they are used in a technical manner, for example in the manufacture of dyes, varnishes, and plastics (Clariant Business Unit Pigments). VIEW ENTIRE GLOSSARY
Pigments are substances used for coloring; they are used in a technical manner, for example in the manufacture of dyes, varnishes, and plastics (Clariant Business Unit Pigments). VIEW ENTIRE GLOSSARY