When Can We Advance the Shift to Renewable Energy?
Environmental Protection and Resources
When Can We Advance the Shift to Renewable Energy?
Renewable energy sources are the future. Their use is taking hold across the globe but also poses new challenges with energy storage and distribution. The chemical industry has an important role to play both as a big energy consumer and by enabling new ways of using and storing electricity.
External Expert Interview
Daniel Teichmann
As CEO of Hydrogenious Technologies, Daniel has set out to finally make using hydrogen for storing and transporting energy easy and safe.
Read the interviewCan catalysis shape the future energy storage?
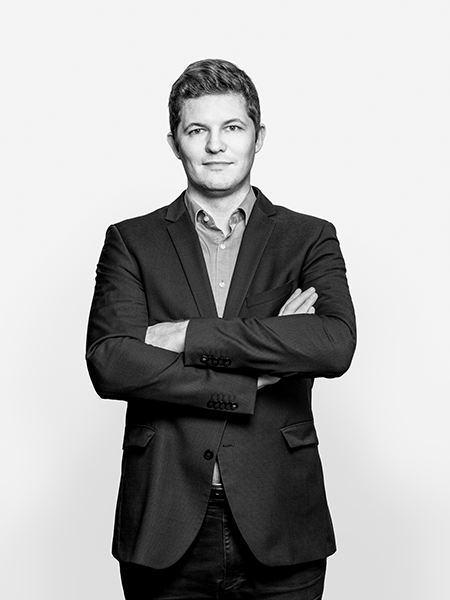
Daniel, hydrogen is often touted as the fuel of the future. Why isn’t our world running on hydrogen?
Hydrogen is a powerful and fully renewable energy carrier. The only emission from using it as fuel is water. That’s why we believe it will play a significant role as fuel for cars and as a way to store energy from renewable sources like wind and solar power. The problem lies with storing and transporting hydrogen, which at normal temperatures has a low density and is extremely volatile. The conventional fix was to either compress it or cool it to very low temperatures. Both methods require elaborate equipment and additional energy.
What is your solution?
We store hydrogen in a liquid by chemically binding it in an oil – our Liquid Organic Hydrogen Carrier, or LOHC.
How do you get the hydrogen into the oil?
We hydrogenate the oil using a catalyst. Basically, we build our hydrogen atoms into the molecule.
What’s the oil in question?
Dibenzyl-toluene, a readily available commodity mostly used to transfer heat in commercial applications.
How safe is LOHC once it’s full of hydrogen?
A demonstration I often perform for TV crews involves dipping a burning torch into a bucket of loaded LOHC. The torch just dies. The oil doesn’t react at all.
You can literally carry your hydrogen around in an open bucket?
Yes. It is non-toxic and not classified as a dangerous good. It is safer than diesel fuel.
What role does catalysis play and what kind of catalyst do you use?
Catalysis is the key to getting hydrogen into the molecule. We use precious metal catalysts from Clariant’s EleMax™ range tailored specifically to our needs.
How is your partnership with Clariant helping?
Efficiency is crucial. That’s why we work with Clariant to further tweak the catalysts and the process. One of the challenges was that we designed our system to extract hydrogen from mixed streams from industry exhausts. That makes it compatible with real-life hydrogen sources but it demands a lot from the catalyst.
How much hydrogen can the LOHC hold?
A cubic meter of LOHC can carry about 57 kilograms of hydrogen. To give you a better sense, a regular fuel tank with 80 liters of LOHC would carry enough hydrogen to travel about 500 kilometers in a fuel cell car.
Could you fill your fuel tank with LOHC to drive your fuel cell car?
That’s certainly the long term goal. It will require, however, a miniaturized version of our technology. At the moment, we’re focussing on large-scale applications, like providing hydrogen to industrial users and large-scale hydrogen refueling stations. Our current technology comfortably fits a 20-foot shipping container. The beauty is that LOHC lets us use existing infrastructure! Our system can work basically anywhere a truck can go. And the resulting LOHC is easy to transport using conventional fuel trucks.
What would a complete LOHC ecosystem for hydrogen cars look like?
A gas station could store loaded LOHC in their conventional underground fuel tanks and de-hydrogenate it on demand. Our home city of Erlangen is the first to open such a refueling station. But we’re also working towards solutions that could de-hydrogenate LOHC right in your car so that refueling would involve simply exchanging unloaded for loaded oil. Heavy-duty vehicles, such as trucks, trains and even ships, are obvious first contenders on the path to an ever more compact system. One of the pilot projects, coordinated by our partner Helmholtz-Institute of Renewable Energy Erlangen-Nuremberg, involves a train running on LOHC.
Internal Expert Interview
Camilla Lang
As Site Manager and Country ESHA for the Nordics region, Camilla helped Clariant’s Swedish sites make the switch to renewable energy.
Read the interviewCan we fill our energy needs sustainably?
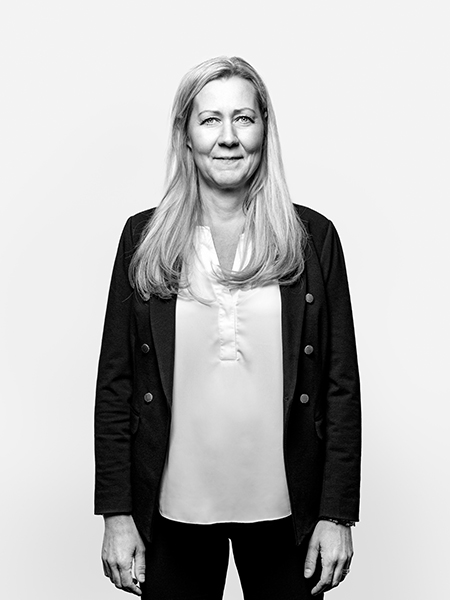
Clariant’s three production sites in Sweden recently switched to renewable energy. Why?
Because it makes a lot of sense. Clariant has set itself global environmental targets, such as to reduce greenhouse gas emissions by 35 percent per ton of produced goods by 2025. Our switch to renewables is a step towards that. The time was right too. We had different contracts with our electricity providers for each of our three sites, and they were all up for renewal. So we decided, first of all, to combine the three agreements and to look for renewable options.
What type of energy were you using and what do you use now?
We switched from mostly nuclear, which still makes up the largest share of Sweden’s electricity mix, to 100 percent hydroelectric power.
How much electricity do the three sites use?
We use around three million kilowatt-hours, and we’ve calculated that we now avoid about 300 tons of CO₂ per year.
What was your role in all this?
I’ve been the site manager for our site in Hällekis since 2011. In 2016, I also took on the responsibility for Environmental, Safety and Health Affairs, or ESHA, in the Nordics region. In this role, I could negotiate a single agreement for all of our three Swedish sites across the business units. I talked to my fellow site managers and management. They were all immediately on board.
Did you face any problems or concerns?
No. It was fairly easy to convince people. We are very conscious of environmental issues in Sweden. And we have a well-working market for renewables. So it was actually very easy to switch.
What about energy costs?
Because of our newly combined purchasing power, we now actually spend less on electricity than we did before.
Is the supply as stable and secure as, say, nuclear power?
We’re connected to the power grid the same way as before, so there are no concerns about stability. We just pay for hydroelectric power. It’s basically the same as when you switch at home. In any case, hydroelectric power is among the most stable renewable sources anyway.
What are some of the other things you’re doing to reduce emissions?
We’re in the process of reducing diesel in our production processes. We still use it mainly in the drying process for bentonite clay here in Hällekis. We’re also looking at our fleet of cars and considering more sustainable options. But, admittedly, we still have quite a way to go in that regard. Still, little things have an impact. Some years ago, we replaced an old engine in our mill here in Hällekis, which now uses only half as much energy as it did before.
Do you think your experience with the switch to renewable energy is applicable elsewhere?
Certainly. There obviously needs to be enough supply and a working market for renewable energy. Then it’s just a matter of, well, just doing it. For us, the timing was right because we wanted to renegotiate our contracts anyway, and I had just taken over my new role for the region. I think that’s a lesson you can take away from it: get different sites and Business Units together under one roof to increase your purchasing power and keep costs down. That may be more difficult in other regions where they operate, let’s say, more independently. And then you need someone or even a small team to take this idea and just run with it.