Where Can We Improve Safety Even Further?
Occupational Health, Safety and Well-being
Where Can We Improve Safety Even Further?
Accidents in the chemical industry are few and far between. That’s undoubtedly a good thing. But it also means that there is less left to learn from mistakes. Managing ever more complex systems and further increasing safety will require a new way of thinking about risks.
External Expert Interview
Martin Clausen
As Senior Risk Engineer at Zurich Insurance, Martin visits Clariant’s chemical sites all over the world to assess risks and further improve safety.
Read the interviewWhere should we look to improve safety even further?
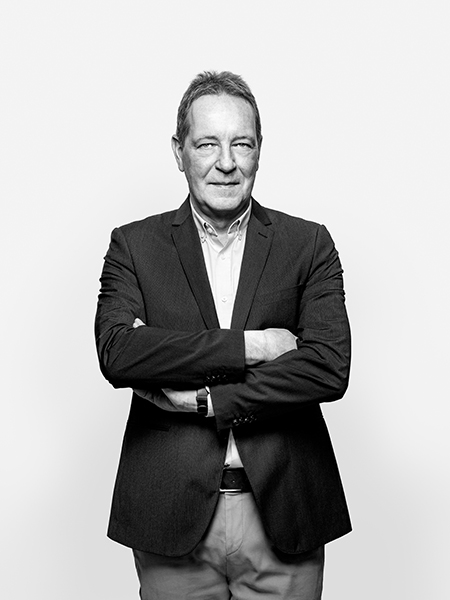
Martin, you’ve just come back from Asia. What were you doing there?
I visited two of Clariant’s large production sites for a risk assessment, one in China and one in Indonesia. Zurich Insurance Group is Clariant’s main global insurer for property and supply chain risks. As a risk engineer for Zurich, I personally visit about ten Clariant sites every year. It’s important to us that we understand the specific risks our client deals with and help find ways to reduce them.
What kind of risks do you assess and how?
I focus on risks to Clariant’s assets as well as their plants and facilities. Risks may involve accidents, fires, natural hazards, and so on that could spell massive losses and potentially interrupt Clariant’s supply chain for days or even months. That’s why my visits are usually to larger sites that play a critical role in Clariant’s supply chain. But occasionally Clariant might specifically ask us to analyze smaller sites, say, if they’re taking on assets from someone else.
Is the chemical industry a risky business?
The industry handles substances that can be very dangerous to humans and the environment. And chemical processes can involve large amounts of energy. All this combined can pose huge risks. It’s paramount that those risks are mitigated effectively and the industry as a whole does this very well. Tight regulation and oversight also do their part.
Are there regional differences?
Not so much. Particularly with a global company like Clariant, which has very high safety standards and a working safety culture, because they establish the same policies and expectations all over the world. That being said, in my job, I find it especially interesting to see how different cultures go about meeting the same goal. And I think it’s important to give teams a certain degree of freedom to do so.
Speaking of goals, the industry as a whole has a record of reducing accident rates further and further. Clariant works towards »zero accidents«. What do you make of that?
Personally, I’m skeptical. A world without accidents is a nice goal to have. A strong focus on ever lower accident rates does help to improve, and we have to learn from what went wrong. But things are more complex from my point of view.
You’ll have to explain.
Think of it this way: Do we really understand new risks we’re dealing with if we mainly learn from past failures? Systems are becoming ever more complex and interconnected. We need to understand and work on what I call »system resilience«. Rather than focussing on what went wrong, we should be asking why things go right. What makes the system in question stable and safe? I believe in looking at the bigger picture rather than chasing numbers.
Are different aspects of safety connected?
Absolutely. A lapse in process safety can have immediate and drastic consequences on all aspects of safety. A healthy safety culture can’t have any blind spots, and laxness in one area usually seeps into others.
What are warning signs when visiting a site?
It literally starts right at the gate. If security is lax, for example, I’m already alert. If the people I’m talking to aren’t prepared, I know there’s trouble.
You say safety is becoming more complex, but is there still a simple golden rule to safety?
I think there are a few life-saving rules in the working environment that we need to enforce with zero tolerance. I’m thinking also about those little shortcuts we’re all attempted to take: Walking a red light, using the phone while driving. That’s the kind of unnecessary risk-taking we need to eliminate. I know of cases where people have been fired on the spot because they called into meetings from their phone while driving.
Internal Expert Interview
Paul Lieck
As Corporate Safety Director North America at Clariant, Paul works to highlight and control everyday risks in the workplace and uphold safety as a core company value.
Read the interviewWhat helps us keep employees healthy and safe?
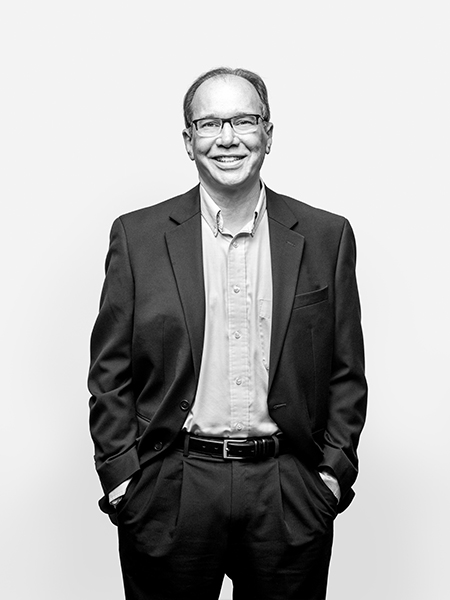
Paul, you’re coming up on 37 years of working in environmental safety and health. What’s your recipe for safety?
There’s not one simple answer to that. I always talk about all the different things that go into it – what we call the elements of safety. You have policies and guidelines at a Group level and then specific procedures at the sites. You need proper training and the appropriate resources. Of course it’s about designing our plants so they can be operated safely. But safety also involves ensuring people have the right skills and attitude towards safety, as well as focusing on safe behaviors. All of these elements are critical to our success.
How important is the right attitude in general?
Awareness among employees and commitment from management are crucial elements of safety. I see that with Clariant. And the commitment goes to the very top. Our former CEO has clearly supported safety, and our incoming CEO made it a key part of his message when he introduced himself to us. To me, that’s fantastic!
So it’s about making safety a priority throughout the company?
I’d go further than that. I see safety as one of our core values. It’s okay to talk about safety being a priority, but it has to go beyond being a priority. A rush order that comes in or other factors may momentarily shift your priorities, but not your core values.
What about you personally?
If you asked my wife and my daughters, they would tell you that safety has been a constant theme around our house for many years. Safety at home was already important to me, but became even more important as our daughters grew, especially when they started driving.
Is driver safety an issue for Clariant too?
Absolutely. Our Business Unit Oil & Mining Services (OMS), for instance, places special emphasis on driver safety. OMS employs a significant number of trucks and drivers to deliver our products to customers, even in very remote places. It not only puts our drivers on the road but often on our customers’ property. So OMS has implemented a program called »SmartDrive« where driving habits are continually evaluated and improved. Additionally, they’ve introduced an effort called »Check 6« to focus attention on checking the condition of each vehicle before use.
Let’s talk numbers! How many accidents have you seen in 2018?
In 2018, the Lost Time Accident Rate or LTAR is 0.16 for Clariant North America.
What does that mean in absolute numbers?
It means that, with over 2 300 employees working well over 5 million hours annually, we’ve so far seen a total of four accidents where people had to miss at least a day at work. LTAR is a common indicator by which the industry measures work safety.
Are there others?
We track so-called OSHA reportable incidents where a person might need to get treatment but won’t have to miss work. Then there are first-aid incidents – starting with even just a band-aid. And we track near misses or »safety deviations« as we call them, where employees report a potentially hazardous situation they’ve witnessed. All this gives us data to work with.
What are the data telling you?
What we see is that we’ve come a very long way in process and work safety. But we have to stay aware of everyday risks. As an example, in 2017, a third of our more significant injuries in North America resulted from slips, trips, and falls. That’s nothing specific to the kind of work we do. But it led us to take action, and already we’ve seen a significant drop in those types of accidents in 2018. Numbers aren’t everything, but they help us focus our attention and raise awareness.
What are some of the more creative ways you’ve seen used to raise awareness?
Our site in Chicago has a great program providing materials that people can take home and even use with their kids. That encourages you to think about safety more broadly. At our site in Phoenix, Arizona, they’ve named the aisle ways in the plant using street signs like »Safety Way«, »Proper Lifting Lane«, or »No-Lost-Time Boulevard«. That’s a new and really innovative way to focus on safety. Awareness is extremely important. Combining this with the other elements of safety is what we have to do to ensure our success in keeping our workplaces safe.