Closing the loop
Contribution to SDGs
This story is an example of Clariant’s contribution to SDG 12 and SDG 17.
Read more in Sustainable Development Goals
-
Ensure sustainable consumption and production patterns
-
Strengthen the means of implementation and revitalize the global partnership for sustainable development
With its new EcoCircle initiative, Clariant is tackling the problem of plastic waste along the entire value chain by building a unique cross-industry network.
Plastic is everywhere. In the century since a Belgian chemist named Leo Baekeland came up with Bakelite™, the first fully synthetic polymer, these types of materials have become ubiquitous and changed almost every aspect of our everyday life. That’s no surprise. Plastics are tough, lightweight, cheap, extremely versatile, and almost imperishable. Sadly, it is this last part in particular that is causing problems. Plastic waste takes decades, if not centuries, to decompose. And despite all of our recycling efforts, only about 16% of all the plastic produced worldwide is recycled. The vast majority is either incinerated or ends up in landfill, unmanaged dumps, or even in the wild. Every year, about eight million tons of plastic leak into the ocean. At this rate, some estimates say, plastic will outweigh fish in the sea by 2050.
In fact, the phrase »plastics are everywhere« has taken on a somewhat ominous meaning. Researchers have recently found microplastic in the food we eat, the water we drink, and the air we breathe. That level of pollution has lent a different image to the wonder material of the past. The good news is that it doesn’t have to stay that way. Most plastic could be recycled. The bad news is that doing so requires a massive shift in the way we produce, use, collect, and reuse it – and Clariant wants to contribute its part to this shift.
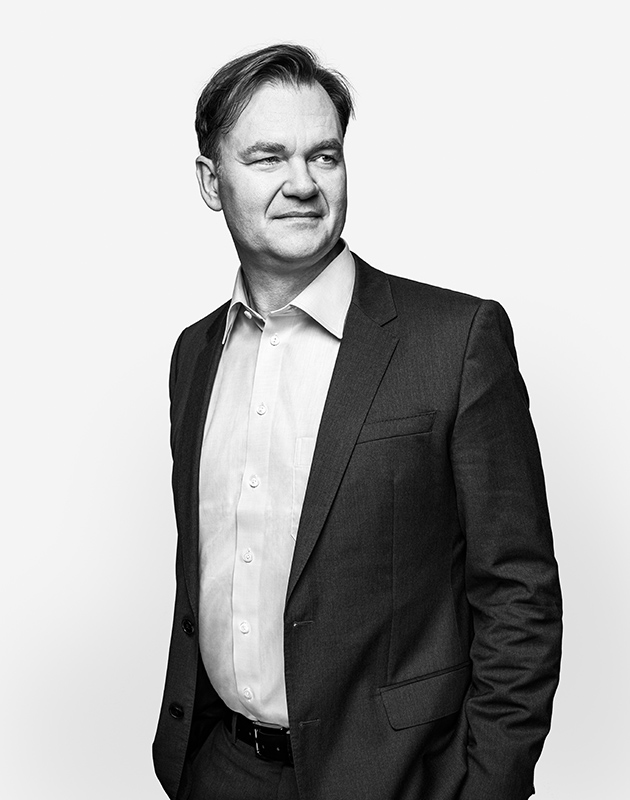
»Humanity desperately needs to solve its waste problem.«
Richard Haldimann Head of New Business Development
»Humanity desperately needs to solve its waste problem,« says Richard Haldimann, Clariant’s Head of New Business Development. For him and many others, establishing a truly circular plastics economy is the way to go. As a leading supplier to the industry with decades of experience in improving plastics, Clariant is certainly wellplaced to do its part. Clariant’s Business Units Pigments, Additives, and Masterbatches supply eponymous products that are essential to the industry. A masterbatch, for example, is a type of concentrate, a polymer with a very specific and highly concentrated mix of pigments and additives, which can be melted into any raw polymer to achieve a desired effect. »Some of our products already help make plastics especially fit for recycling or can enhance the performance of post-consumer recyclates,« says Haldimann. But when it comes to plastic packaging, for example, Clariant is just a single link in a complex value chain that involves everybody from polymer producers and converters, who manufacture the actual packaging, to brand owners and retailers, and ultimately consumers, waste collectors, and recyclers. »They all have very different requirements,« says Haldimann. »However, one cause they all increasingly rally around is the push for a truly circular economy.« That’s why Clariant initiated what it calls its »EcoCircle,« an initiative to jointly develop new materials and technologies with the whole value chain in mind. »With EcoCircle, we bring together very different stakeholders across several industries,« says Bettina Siggelkow, who manages these collaborations at Clariant. Siggelkow is herself not only a chemist but also an expert in collaborative techniques and joint R&D. She was involved in introducing modern approaches such as design thinking to Clariant’s own innovation work. »I’ve had many jobs within Clariant. One thing they all involved was orchestrating people from very different fields,« she says.
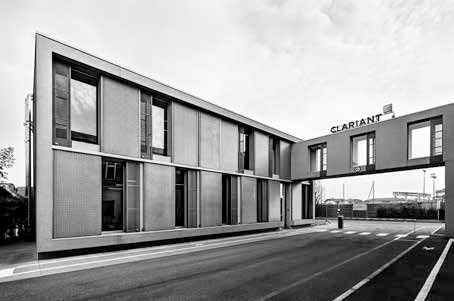
Future address
Clariant’s site in Pogliano, Italy, is home to the company’s first so-called EcoCircle Center of Excellence.
Identifying problematic plastics
At the triennial K 2019, the world’s largest plastics expo in Duesseldorf, Germany, Clariant and a host of its EcoCircle partners recently demonstrated what these collaborations bring to the table. One of the projects presented at the expo was Clariant’s cooperation with TOMRA Sorting Recycling, a Norwegian company that is an industry leader for the type of instruments that enable automated sorting. The collaboration tackles a common problem with dark or black plastic packaging. These have become immensely popular in recent years for anything from shampoo bottles to the housing of consumer electronics, but that has proven problematic for recycling centers. Conventional black pigments such as carbon black do not reflect near-infrared (NIR) light. That renders them invisible to the kinds of NIR scanners that recyclers commonly rely on to automatically identify and pick out plastics in the waste stream. Under NIR, any plastic bottle cap, shampoo bottle, or food container tinted with carbon black is simply indistinguishable from the conveyor belt it moves on. As a result, these plastics are lost to recyclers and either end up in landfill or are incinerated. To end this, Clariant developed – and TOMRA successfully tested – a new additive masterbatch called CESA® IR that enables the detectability of black plastics for recycling and is also itself recyclable.
The role of additives in recycling can be tricky. While some, such as Clariant’s new CESA® IR, help in the process, others can have adverse effects. That was a problem for another of Clariant’s EcoCircle partners. APK, a young company from Merseburg near Leipzig, has developed a unique solvent-based recycling technology they’ve dubbed Newcycling™. It allows APK to dissolve certain plastics from waste and then extract the desired plastic from the solution in its pure form. That puts the technology somewhere between mechanical recycling, which relies on melting shredded plastic but almost never yields perfectly pure material, and chemical recycling, which delivers quasi-virgin plastic via depolymerization but requires large amounts of energy. »In working with APK, we’ve already learned a lot about what types of impurities, additives, and pigments in the waste stream can gum up their process,« says Siggelkow. »And together, we’ve come up with new ways to purify and reuse their solvent after each cycle, which makes the process very efficient.«
Biotransformation
An end to fugitive plastic
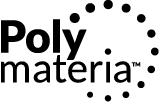
While EcoCircle, as the name suggests, is devoted to recovering and reusing as much plastic as possible, the risk of plastic leakage into nature always remains. And not just in regions where waste collection generally leaves a lot to be desired. To tackle this problem, Clariant joined forces with Polymateria in 2019 to bring its unique innovation to market. The British start-up has developed a »biotransformation« technology that alters the properties of commonly used plastics to make them entirely biodegradable after a predetermined time. Applied as an additive, Polymateria’s solution remains dormant for the specified shelf life of the packaging, which can range from six months to three years. »That way, our technology gives recycling every chance to happen,« says Niall Dunne, Polymateria’s CEO. »But if any of the material does find its way out into the wild, our technology is the only one that is able to achieve full biodegradation – in water, CO2, and biomass – for the most highly littered forms of plastic.« Polymateria’s solution avoids creating microplastic by attacking the hard crystalline structure of the polymer, making the molecules bioavailable again. Additional prebiotic activators even draw in and stimulate microorganisms to feast on the carbon molecules.
Effective additives after numerous cycles
The best-case scenario, however, is for additives to actually be part of the recycling process and maintain their beneficial effect throughout several cycles of reuse. That is something Clariant has specifically worked on for its range of Exolit® OP flame retardants. These are phosphorus-based, non-halogenated flame retardants that are commonly used for plastics in electronics or cars. Together with the Fraunhofer Institute, an independent German research center, Clariant was able to show that the Exolit® range also maintains its flame-retardant property even after being recycled multiple times. That is a huge boon to sustainability because it allows the likes of circuit board producers or automotive suppliers to recycle their own waste and regrind material for the same application.
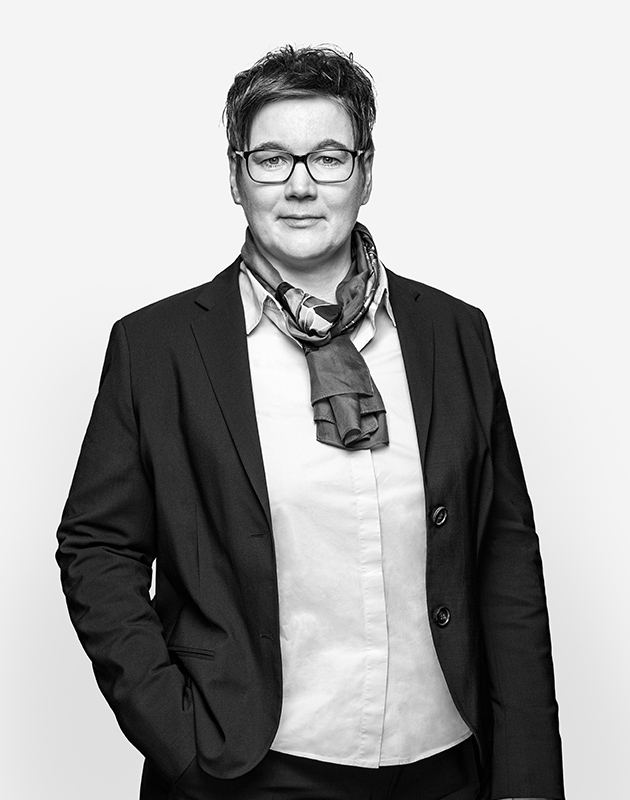
»Consumers, retailers, and brand owners are all pushing to close the plastics loop.«
Bettina Siggelkow EcoCircle Program Manager, New Business Development
The business case for recyclable materials and what Clariant calls »design for recycling« is straightforward. »Consumers, retailers, and brand owners are all pushing to close the plastics loop,« says Siggelkow. Various brands have committed themselves to using 100% recyclable materials by 2025, increasing the amount of recycled polymers in their products to up to 25%, partly even up to 50%. And retailers, who up until recently mostly cared about things like shelf life, stackability, and sturdiness, now look to do their part by reducing waste and recycling more packaging themselves. Big industry names are even themselves getting involved along the entire value chain. »We see brand owners and retailers opening up their own labs and buying up recyclers or start-ups,« says Haldimann.
For Clariant, moving up the value chain to talk directly with brand owners is nothing new. Its ColorWorks™ team has established ties within the industry to work and advise on coming trends. With the industry now looking for trends and innovation in terms of recycling and circular solutions, Clariant sees itself involved with even more stakeholders.
Joint efforts with EcoCircle partners have already yielded new products, some of which are marketed with the suffix »Circle« to promote their benefit to the circular plastics economy. But EcoCircle is about much more than product development. Clariant is building a platform and a network to work on R&D and new industry standards together with stakeholders. Only very few of those will ever be direct customers to Clariant. »It’s much more about supporting the transition from single-use plastic to a truly circular plastics economy,« says Haldimann. »The industry and its stakeholders can undoubtedly benefit from our products along with our know-how, whether it’s for virgin polymers or for recyclates. That’s one reason why we’re confident about the size of those respective markets.«
Global plastic production has increased more than twentyfold in the last half century. It is set to at least triple again by the middle of this century. With all the negativity surrounding plastic, that might seem daunting. But it’s easy to forget the positive impact plastic has. Better plastic packaging has dramatically decreased food waste, lightweight plastic packaging saves fuel in transportation, and plastic use for medical equipment has helped immeasurably to make medical treatment safer and affordable. »Plastic is here to stay. What will change is the way it’s produced and reused,« says Haldimann.
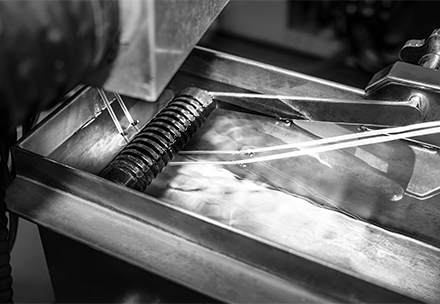
Producing
Developers in Pogliano already use industry-standard equipment to produce different plastic materials.
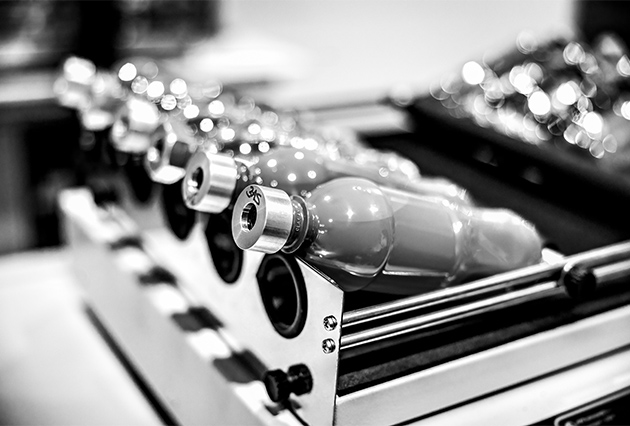
Using
Clariant has decades of experience in tailoring material properties to fit any application imaginable.
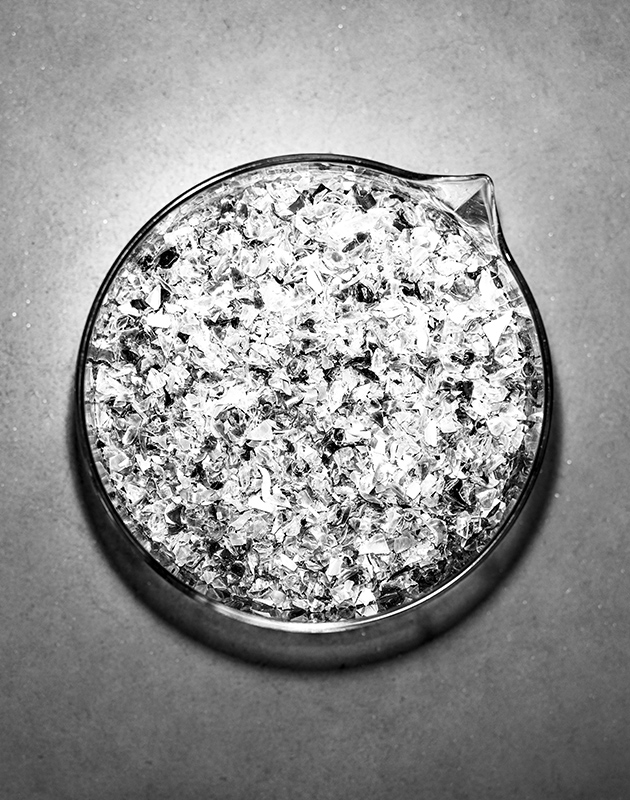
Recovering
Shredding plastic waste is one step in the small-scale recycling process.
Tackling real-life problems
EcoCircle, which so far has been an umbrella term for a range of ongoing R&D projects, meetings, and roundtables, will soon have its own dedicated research facilities. At its Masterbatch site in Pogliano, Italy, Clariant is building the first of what it calls »EcoCircle Centers of Excellence.« Here, Clariant is establishing a kind of small-scale recycling center that, together with already existing labs, will eventually replicate the entire process from waste shredding to washing, recycling, and finally converting recyclates back into actual products. »In Pogliano, we’ve been working for some time now with industry-standard extruders and production equipment that our direct customers use,« says Siggelkow. »Now we’re expanding to what comes before and after.« The aim is to come up with solutions that tackle real-life problems for anyone recovering and reusing plastic materials, both by mechanical recycling as well as chemical recycling. To address other areas of recycling, Clariant is currently investigating the setup of additional Centers of Excellence.
Clariant’s Business Unit Additives, in particular, is set to improve recycling not only in the packaging industry. One recent innovation involves carpets. In Europe alone, about three-quarters of all carpet flooring eventually is sent to landfill or incinerated – even though most carpets today are made with recyclable woven or tufted materials. The problem is the latex backing, which usually cannot be removed from the fibers and makes for a nonrecyclable mix of materials. With Licocene®, Clariant’s Business Unit Additives offers recyclable adhesives that also save water and energy in their application. More importantly, they can be separated from the fibers easily and cleanly by using a process called CreaSolv™, developed by the Fraunhofer Institute. It recovers the adhesive with at least 90% of its virgin quality for reuse and has the potential to close the plastic loops for yet another industry.
SWITZERLAND & ITALY
The value chain describes the series of steps in the production process, from raw materials through the various intermediate stages to the finished end product. View entire glossary
Pigments are substances used for coloring; they are used in a technical manner, for example in the manufacture of dyes, varnishes, and plastics. View entire glossary
A substance added to products in small quantities to achieve certain properties or to improve a product. View entire glossary
These are plastic additives in the form of granules with dyestuffs or other additives used to dye or alter the properties of natural plastic. View entire glossary
Stakeholders are people or groups whose interests are linked in various ways with those of a company. They include shareholders, business partners, employees, neighbors, and the community. View entire glossary
A substance added to products in small quantities to achieve certain properties or to improve a product. View entire glossary
Pigments are substances used for coloring; they are used in a technical manner, for example in the manufacture of dyes, varnishes, and plastics. View entire glossary
The value chain describes the series of steps in the production process, from raw materials through the various intermediate stages to the finished end product. View entire glossary
Stakeholders are people or groups whose interests are linked in various ways with those of a company. They include shareholders, business partners, employees, neighbors, and the community. View entire glossary
These are plastic additives in the form of granules with dyestuffs or other additives used to dye or alter the properties of natural plastic. View entire glossary