Service Succeeds
Contribution to SDGs
This story is an example of Clariant’s contribution to SDG 9 and SDG 12. Read more in Sustainable Development Goals
-
Build resilient infrastructure, promote inclusive and sustainable industrialization and foster innovation
-
Ensure sustainable consumption and production patterns
How a specialist team of engineers at Clariant’s Business Unit Catalysts provides game-changing technical service all across mainland China.
When Donny Yuan joined Clariant in 2015, he had already spent more than twelve years working in different petrochemical productions, mostly for styrene producers, including some of the biggest names in China. But even though catalytic dehydrogenation is at the heart of this type of industrial chemistry, Yuan still had a lot to learn about catalysts themselves. »So when Clariant hired me to provide technical service for their entire range of catalysts, I delved deep into Catalysts’ technology,« Yuan says.
Fast forward five years and Yuan now heads Clariant’s regional Catalysts Engineering Services in China, a team of ten technical engineers spread over four locations across mainland China. Donny Yuan himself sits in Shanghai. Although, as he explains, he spends most of his time neither sitting nor in Shanghai. »About 60% of my work involves meeting customers, checking in on sites, and troubleshooting production issues out in the field.« His business trips take him all around China. The sheer size of the country means that visiting one such business can easily involve a five-hour flight followed by another couple of hours on trains or in the car. »Petrochemical production centers are often located far away from major cities. And we’ve had cases where some of our guys have stayed at a customer site for more than a month,« Yuan says. But to him and everyone on his team, going the extra mile is part of Clariant’s approach to providing its technical service.
Clariant’s Business Unit Catalysts operates globally but stresses its regional focus. Close to 1 800 people worldwide work for the Business Unit. It runs a total of 14 production sites, 20 sales offices, and just as many offices for Engineering Services around the world. Proximity matters. »Each region has very different needs,« says Roger Long, Clariant’s Regional Marketing Manager for Catalysts in China and Asia-Pacific. Take feedstocks, for instance. While chemical production in Europe and the Middle East relies mostly on natural gas or petroleum, and the USA are heavy on shale gas, most of China’s producers use derivatives from coal. »The applications are similar, but the processes are totally different,« Long explains. »So our Engineering Service here in China deals with catalysts that are tailor-made specifically for this type of feedstock.«
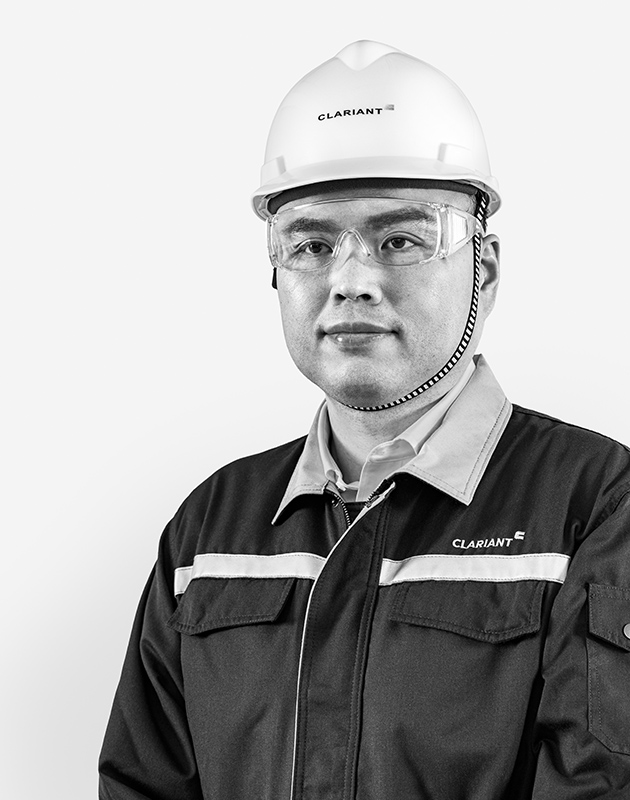
Donny Yuan
Head of Engineering Services China, Business Unit Catalysts
CHINA
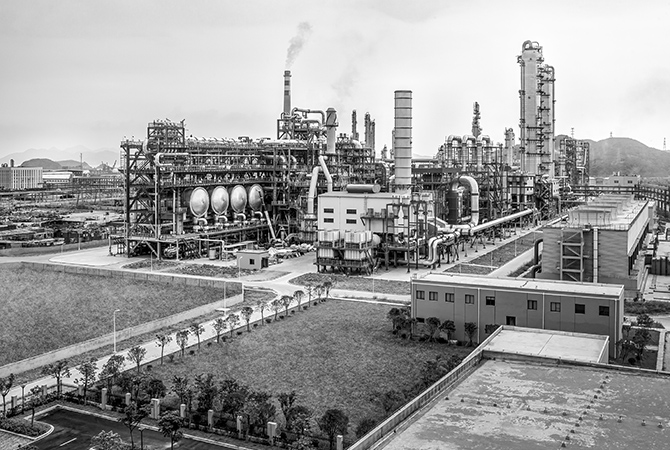
Creating value
Plants using Clariant’s CATOFIN™ process prove reliable and efficient.
Service helps seal the deal
Yuan and his team of technical engineers serve more than 100 current customers at any given time. Additionally, they are called upon whenever their expertise is needed elsewhere in the world. They themselves can rely on the rest of the global network for backup too. Engineers like Yuan are involved early on in any commercial bidding. »We attend all the initial technical meetings with the customer and, for example, help select the right catalyst for their needs,« Yuan explains. More often than not, these technical discussions are actually what helps seal the deal. Yuan, his fellow engineers, and the service they provide over the entire lifetime of a catalyst are an essential part of the product offering.
Catalysts are crucial to almost every chemical production. By reducing the energy required for a certain reaction or helping to achieve higher yields with fewer by-products, catalysts are a key to both productivity and efficiency. In fact, many of the reactions used industrially today would be either uneconomical or physically impossible without specialized catalysts. »For producers, getting the optimal performance out of a catalyst can have a massive impact on their bottom line,« says Long. »Still, not too many companies provide our level of service. We are one of the few catalyst providers among our peers to have as many as four Engineering Service offices in mainland China. And today, we are the only one with such an office in Yinchuan in the Northwest, the very heart of China’s coal-to-chemicals industry.«
New offices
Help is just around the corner
A new Engineering Services office in Jakarta, Indonesia, brings Clariant’s Business Unit Catalysts even closer to its regional customers.
In the second half of 2019, Clariant’s Business Unit Catalysts opened a brand-new office for engineering services in Indonesia. It follows on the heels of similar new offices in Singapore and Japan, bringing the total to 20 worldwide. The expansion is aimed at enhancing regional support, particularly in southern countries of Asia-Pacific. Technical services here has a strong focus on catalysts for ethylene and styrene as well as syngas applications, distillate upgrading, hydrogenation, and oxidation. Inaugurated in September, the new Indonesian office is based at Clariant’s site in Tangerang, near the capital Jakarta. Clariant already operates a joint-venture catalyst production facility near Jakarta, in Cikampek. The catalyst specialists appointed for the new service office will work closely with their regional colleagues.
Whenever Clariant wins a commercial bidding, that’s usually when Yuan and his team really jump into action. »Loading the reactor and starting the process is the most crucial phase for any catalytic process,« Yuan explains. His team advises and trains the production crew on how to first get the catalyst into the reactor. Some of that happens in an actual classroom setting, and some of it on the job. »Customers will arrange for field operators, production crew management, and engineers to take part in these training courses,« says Yuan. »Even the engineers, who are absolute experts in their field, can’t always know how they need to handle our product and why.« That is why Clariant provides a manual on how to load and use its catalysts and has developed a patented loading system together with the necessary equipment.
»Getting the distribution right and making sure the catalyst isn’t damaged determines how efficiently you’ll be able to run your production for the next couple of years,« Yuan explains. For example, Clariant puts a lot of effort into maximizing the performance of its catalysts, not least by producing them in specific shapes such as pellets, tables, or extrusions that optimize the available catalytic geometric surface area (GSA). For certain kinds of catalysts, dropping these from the top of a tall reactor would wreak havoc on those surfaces. »That’s why we make sure the catalyst is loaded layer by layer and its integrity is protected at all times,« says Yuan. The whole start-up process can take up to three weeks depending on the application.
Pleased customer
»Fast, smooth, and successful«
Clariant helped its customer Chinese Hengli Group to initiate its latest groundbreaking production.
Some major start-ups of catalytic productions make headlines in the industry. Like when, in the summer of 2019, Clariant announced the successful start-up of its CATOFIN™ catalyst for the Hengli Group, one of China’s largest petrochemical suppliers. Their new mixed-feed dehydrogenation plant in Dalian is designed to process 500 000 annual tons of propane and 800 000 annual tons of isobutane to produce over a million tons of propylene and isobutylene. That makes it the world’s largest plant to use Clariant’s CATOFIN™ catalyst technology and a major milestone for the industry. »We are very proud of our achievements with respect to this groundbreaking project,« says Guangqin Peng, Chief Engineer of Hengli Petrochemical (Dalian) Refinery Co Ltd. »The fast, smooth, and successful start-up of this unit would not have been possible without reliable and experienced partners like Clariant.«
What process data reveals
Once production is up and running, Yuan and his team transition into operational support and ongoing performance evaluation. They visit key customer sites every few months but call each and every customer at least once a month to talk shop. Using specialized analytic programs, they review the data provided by the customers, which allows them to draw conclusions about how the catalyst is performing and whether the whole setup is working within the parameters the customer prescribed.
Yuan remembers one incident where a customer notified him about a sudden drop in performance, or rather a growing disparity between input and product yield. He and his team immediately got to work analyzing the latest data. »We used heat balance and material balance calculations and were eventually able to pinpoint that there had to be a mechanical failure, a leak in hydrocarbon supply,« Yuan remembers. In other words, the customer was losing input but, as the data showed, not in the process itself. The customer chose to wait for scheduled maintenance and to proceed with production. »We helped him optimize the feed and process parameters for the changed conditions. That way, we could ensure the stability of the plant operation and also secure the service life of the catalyst,« Yuan says. »In the end, it saved our customer at least another 10% in capacity.« When the customer eventually stopped production and went in to check, sure enough, they found the leak that Clariant’s team had suspected.
When troubleshooting catalytic processes, time is of the essence. Unforeseen changes in the feed or even a complete stop in production can do irreversible damage to the catalyst unless the operators take protective measures. »For some processes, if the feed or the steam cut out, you need to move quickly and protect the catalyst from water or air,« Yuan explains. »Otherwise, you risk poisoning your catalyst within a matter of hours.«
A business like no other
Yuan, like many in the industry, talks of catalysts as if they were living, breathing things. That comes with the trade: Catalysts can be fickle. Treating them right helps them excel at their job, while neglecting them can shorten their lifespan. They can be »poisoned« and »die.« That is not the only way in which the catalyst business differs from others that deal in commodities or raw materials.
»A typical catalyst stays in service for two or three years, but there are a lot that run for five to six, some even for ten and up to 15 years,« Yuan explains. Clariant guarantees technical support throughout the entire service life of a catalyst. »Those are very long-standing customer relationships built both on trust and experience,« Yuan says. He has worked with some of his counterparts on the customer side for years. »You really get to know and understand how they operate. That allows us to anticipate what they might need, and having worked together for such a long time also helps you get to the point very fast.«
»You really get to know and understand how your customers operate.«
Donny Yuan Head of Engineering Services China, Business Unit Catalysts
Each phase of a catalyst’s service life has its own set of rules. Towards the end of its life, for example, a catalyst will usually achieve lower yields but will run especially stable. »That is if you run it correctly,« says Yuan. »But in some very competitive markets, for example, companies might be pushed to run the plant very hard: They change their schedules a lot, or run an aging catalyst at a higher feed while business is good,« says Yuan. That’s when he gets 3 AM phone calls, saying: »You need to come in right away!«
Having the necessary know-how to deal with many different emergency scenarios, the commitment to maintaining optimal performance over the entire service life, and the manpower to do all that for every customer anywhere in China – those are some of the attributes that make Clariant’s work exceptional. But an important factor is not just what Yuan and his fellow engineers do at Clariant but also what they did before. Every one of them has at least five years of experience working in chemical production. »They can talk to customers in their language,« says Yuan. And it shows. »When I was in production and dealt with catalyst suppliers, they would go on and on about their product. We don’t do that. We talk about the process and what the customer needs. We understand what they’re dealing with and help them achieve what they’re trying to do.«
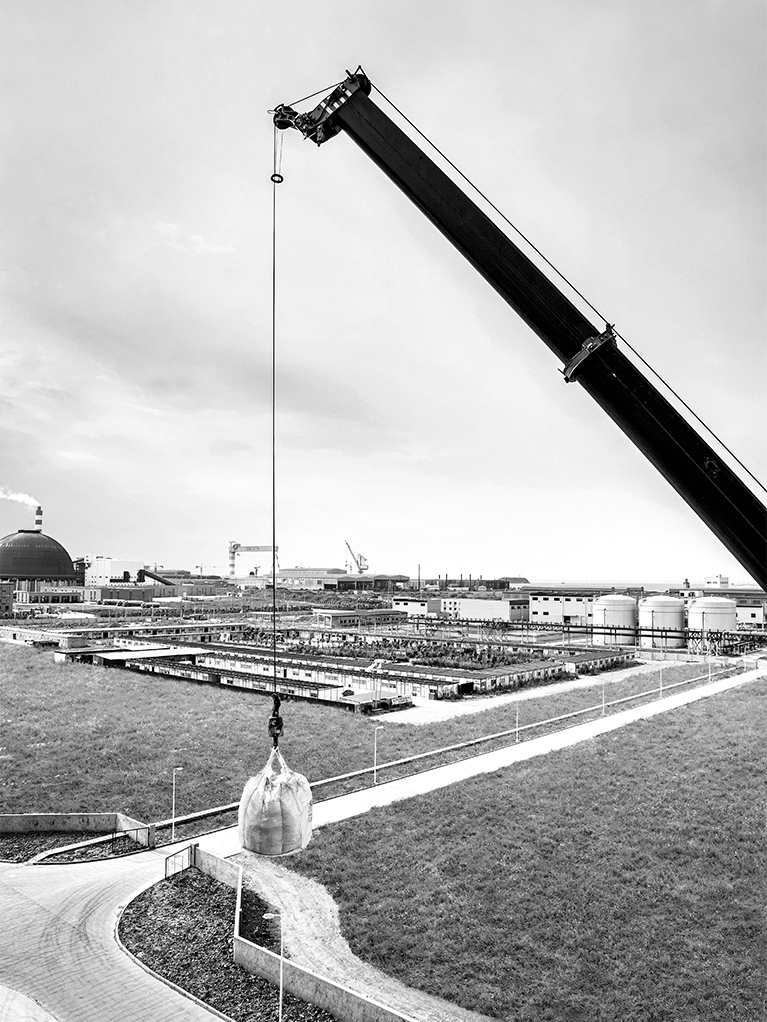
Crucial delivery
Processes for the chemical industry revolve around catalysts. In some cases, that means they need to be lifted into reactors at the heart of production facilities.
A substance that lowers the activation energy, thereby increasing the rate of a chemical reaction without being consumed by the reaction itself. View entire glossary
A substance that lowers the activation energy, thereby increasing the rate of a chemical reaction without being consumed by the reaction itself. View entire glossary
Joint ventures are all activities in which Clariant is involved with another partner. The accounting method applied for joint ventures depends on the specific conditions of the participation. View entire glossary