1. Natural Capital
Clariant is steadfast in its commitment to continuously improve operational efficiency by developing solutions to environmental challenges. Since Clariant’s production depends on ongoing access to many raw materials, stewardship of these natural resources is vital. To reliably and efficiently monitor environmental impacts from its production sites, Clariant regularly validates and reports the environmental data from its largest sites, which cover approximately 95% of production volume. Clariant tracks the smaller sites as well by collecting their environmental data every three years. In 2019, 80 of the 118 production sites, as well as 5 administrative sites, were included in the reporting.
In 2019, Clariant managed to reduce almost all resource intensity figures and is still well on track to achieve its 2025 environmental targets. SEE FIGURE 001, SEE FIGURE 002 Due to the planned divestments of its Masterbatches and Pigments businesses and related effects on the production and the product portfolio, Clariant will revise its environmental targets.
001 ENVIRONMENTAL TARGETS 2025 in % (per t produced goods)
Customer to Cash
1.1. Progress toward environmental targets 2025
Clariant has set goals to achieve significant environmental impact reductions in six crucial areas by 2025, as compared to 2013. In relation to produced goods (per ton), Clariant aims to reduce energy consumption and direct CO2 emissions by 30%; greenhouse gas emissions, water consumption, and waste volume by 35%; and wastewater volume by 40%.
In 2019, energy consumption per ton of produced goods decreased by 2.5%, from 739 kWh to 720 kWh. Direct CO2 emissions (Scope 1) and greenhouse gas emissions (Scope 1 & 2) were reduced from 98 to 89 kg (– 9.2%), and from 215 to 198 kg (– 7.9%) per ton of production, respectively. The reduction in emissions indicates Clariant’s shift to cleaner energy sources, such as natural gas and purchase of green electricity.
Water consumption per ton of produced goods decreased by 7.9%, from 11.3 m3 to 10.4 m3. This reduction was mainly due to water efficiency improvement at many sites and changes in site ownership. Wastewater generation per ton of production diminished by 3.4%, from 2.9 m3 to 2.8 m3.
Waste generation increased by 10.5% in 2019, rising from 53.3 kg to 58.9 kg per ton of production. This significant increase was mainly due to increased generation of non-hazardous gypsum waste generated as sludge during wastewater treatment in a few bentonite processing sites.
002 PROGRESS TOWARDS 2025 TARGETS
1.2. Environmental protection and resources
For Clariant, environmental protection and resources encompasses both the consumption of resources, such as energy and water, and the prevention of pollution and ecosystem effects. To minimize the company’s impacts on the environment and safeguard natural resources, top management attention and a corporate culture that prioritizes environmental stewardship throughout the company are essential.
In 2019, Clariant recognized enhanced interest and focus by investors, customers, and other stakeholders regarding sustainability topics such as plastic recycling and water efficiency improvement, confirming Clariant’s commitment to implement various measures throughout the company and engage in sustainable product development.
|
Continuing |
Discontinued |
Total 20192 |
2018 |
Change |
|||||||||
---|---|---|---|---|---|---|---|---|---|---|---|---|---|---|
|
||||||||||||||
Total energy consumption (in m kWh) |
2 400 |
652 |
3 058 |
3 209 |
–4.7 |
|||||||||
Energy consumption (in kWh/t production) |
601 |
2 547 |
720 |
739 |
–2.6 |
|||||||||
Total water consumption (in m m3) |
25.7 |
17.3 |
44.3 |
49.0 |
–9.6 |
|||||||||
Total wastewater generation (in m m3) |
6.7 |
3.7 |
11.9 |
12.6 |
–5.6 |
|||||||||
Total quantity of waste (in thousand t) |
215.7 |
32.6 |
250.2 |
232 |
7.8 |
1.2.1. Energy
Clariant aims to continually reduce energy consumption and to minimize energy-related greenhouse gas emissions. In 2019, energy consumption per ton of produced goods decreased by 2.5%. Clariant will continue to work toward its energy consumption reductions targeted for 2025 by further investing in and developing programs such as eWATCH™, Clariant Operational Excellence, and the Clariant Production System Yield, Energy, Environment (YEE) initiative.
Through eWATCH™, Clariant crafted a comprehensive energy efficiency program that analyzes energy consumption across operations and identifies potential cost-saving opportunities. Since 2013, a total of CHF 37.3 million was saved by implementing energy efficiency measures and energy-purchasing optimizations. In 2019 alone, Clariant managed to save CHF 4.4 million.
In 2019, Clariant advanced the »eWATCH™ goes digital« initiative. In its production sites, energy management systems and smart meters were implemented to enhance data availability. In order to increase visualization capabilities, Clariant used tools such as Microsoft Power BI, which helped to quickly spot improvement potential or identify outliers. Further, Clariant introduced a monthly energy performance indicator reporting on site and country level.
Optimizing energy consumption with eWatch™
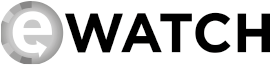
eWATCH™ oversees all forms and usages of energy at Clariant – electricity, heating and cooling, steam, natural gas, nitrogen, and the production of deionized water – by taking into account the design and setup of equipment and processes across Clariant’s facilities. It also records and analyzes Clariant’s energy consumption, including information on energy flows, prices, and usage optimization. It maintains information on total energy usage patterns and requirements and will increasingly consider maintenance activities, changeovers, cleaning, and production planning and scheduling in the future. eWATCH™ focuses on three pillars: operations and technology; awareness, mindset, and behavior; and energy management.
Clariant globally passed the recertification of the energy management system according to ISO 50001 and prepared for the updated standard in various sites. 39% of Clariant’s production volume was produced at sites certified with ISO 50001. Clariant also continued performing energy benchmarks of utility generation systems internally as well as against state-of-the-art installations.
The Production System YEE initiative analyzes Clariant’s production processes and units to discover even more opportunities to increase yields, improve energy efficiency, and reduce waste streams. Since its inception in 2012, Clariant achieved savings of CHF 80 million due to YEE. In 2019 alone, savings amounted to almost CHF 6 million.
1.2.2. Water consumption and wastewater generation
Water is one of the most important auxiliary materials for the chemical industry. Clariant considers the entire volume of water withdrawn and used as its total water consumption. Cooling water returned to the source after being used in cooling cycles is not excluded from total consumption. Clariant uses roughly 70% of purchased water for cooling production plants, 20% for production processes, and 10% as a product component or for sanitary purposes. In 2019, water consumption per ton of produced goods decreased by almost 8%. This reduction was due to water efficiency improvement measures, changes in site ownership, less water-intensive production processes, and a decrease of production volume in sites with high water consumption.
Wastewater is well managed at all Clariant production sites, and local regulatory requirements regarding discharge limits are strictly followed. The company assesses wastewater quality by measuring heavy metals concentration, nitrogen and phosphorus compounds, as well as biological and chemical oxygen demands. Wastewater is often pretreated at Clariant’s sites before being transferred to dedicated industrial or municipal wastewater treatment plants for further treatment. The pretreatment mostly consists of a multistage chemical and physical treatment to ensure effluents do not impair the receiving water bodies. With this multistep treatment approach and constant monitoring, Clariant guarantees that discharged wastewater does not negatively impact ecosystems. In 2019, wastewater generation per ton of produced goods decreased by 3.5%.
Two years ago, Clariant undertook a Group-wide water-risk assessment employing the World Resources Institute’s (WRI) global risk assessment tool. The assessment showed that only a small percentage of Clariant’s sites are located in water-risk areas. To further deepen the understanding of risks, a pilot water-risk assessment project was completed in Santa Clara, Mexico, in 2018. Several water efficiency projects were implemented on the site, which included harvesting rainwater for cooling purposes, reducing water consumption in various production steps, and implementing a water pressure system in filter press areas. In addition, upgrading the existing wastewater treatment plant to enable reuse of treated water is being investigated. In 2019, analogous water-risk assessment studies were performed at all Clariant sites located in water-risk areas. These in-depth analyses will be used to develop water management goals that ensure the respective sites can responsibly manage their risks. Clariant’s comprehensive and continued efforts in water-risk management at different levels of the organization resulted in outside recognition. In the Dow Jones Sustainability Index (DJSI), the company was one of the best-in-class performers in its sector regarding water-related risks for the third consecutive year.
Clear goals
In 2019, Clariant opened a new wastewater treatment plant at its production site in Bonthapally, India. The facility at the zero liquid discharge site has the capacity to treat 300 000 liters of wastewater per day. It employs a state-of-the-art combination of highly efficient processes that remove any contamination and purify the water in various stages to be potable as per World Health Organization (WHO) guidelines. The process involves biological treatment, ultrafiltration, reverse osmosis, multiple evaporation techniques as well as agitated thin-film drying. The investment in the new wastewater treatment plant is part of the company’s growth strategy for its Business Unit Industrial & Consumer Specialties (ICS), and it ensures the company’s continued focus on sustainability and environmental protection. The ICS site in Bonthapally has been awarded a rating of three stars out of three for its Environment, Health, and Safety (EHS) practices in 2018 by the Confederation of Indian Industry, Southern Region.
1.2.3. Waste
Clariant follows a strict waste-management protocol. The company prioritizes waste prevention as this approach minimizes resource consumption in addition to costs. During product development and manufacturing, Clariant aims to generate as little waste as possible, and any unavoidable waste is recycled or disposed of properly in adherence to local regulations. Accumulated waste is documented in detail in order to enable proper classification and handling. Per ton of production, generation of waste increased by 10.5% in 2019. This was mainly due to an increased generation of non-hazardous gypsum waste generated as sludge during wastewater treatment in a few bentonite processing sites, and the removal of out-of-date inventory such as old equipment.
1.2.4. Air pollution
Clariant also judiciously monitors and contains air emissions from operations. Clariant adheres to local regulations regarding air emission limits in all the countries in which it operates. Air pollutants tracked at the Group level include volatile organic compounds (VOCs), sulfur oxides (SOx’s), and nitrogen oxides (NOx’s).
1.2.5. Ecosystem protection
Clariant strives to ensure its activities do not impede or degrade ecosystem services, such as provision of fresh water, air purification, energy production, and protection against natural disasters, as they are vital for its businesses and society in general. Clariant does not operate production sites in biological reserves or areas with high biodiversity value.
SPOTS
The Sustainable Palm Oil and Traceability in Sabah (SPOTS) aims to support small Malaysian palm oil producers with regard to sustainability, certification, and supply chain traceability, and to increase productivity by 20% until 2020. clariant.com/en/Sustainability/Value-Chain-Collaboration/ The-SPOTS-Initiative
To protect rainforests and peatland and combat ecological degradation caused by the clearing of land for palm oil plantations, Clariant also considers impacts of specific raw materials used and pursues certification of its palm oil derivatives supply. As a member of the Roundtable on Sustainable Palm Oil (RSPO), Clariant achieved mass-balance certification for all of its sites in 2016 and has more than 200 products, which are available with the Mass Balance certificate. Clariant will continue to extend the certified product portfolio in order to help its customers meet demand for certified palm ingredients.
When mining bentonite, Clariant follows several steps to exceed societal and community expectations regarding the conservation of the surrounding ecosystem. Before drilling begins, Clariant’s geologists craft a plan to minimize associated environmental impacts. This includes removing the topsoil and overburden as carefully as possible in order to preserve it for future land restoration. During mining, Clariant ensures that resident animals may easily move to adjacent areas. Before being transported, the bentonite is sun-dried, reducing its weight and thus emissions produced in shipping. Quarry closure is undertaken with local experts in order to restore the land for profitable use in forestry or agriculture. These efforts are crucial to maintain healthy relationships with local communities and protect local ecosystems.
GRI Online Report
Management Approach Environmental Protection and Resources Material Topics – Focus
1.3. Climate change
Climate change is one of society’s most significant challenges and is driven by the emissions of greenhouse gases. As impacts magnify, such as shifting weather patterns and increased risk of flooding, attention rises and calls for actions accordingly.
For an innovative chemical company like Clariant, climate change triggers both risks and opportunities. For example, while more governments are introducing carbon pricing schemes, business opportunities to reduce energy costs and the development of low-carbon products, such as catalysts that support the reduction of greenhouse gas emissions, are to be exploited.
In order to contribute to a sustainable economy, Clariant adopted environmental targets to be achieved by 2025. Compared to the base year 2013, Clariant committed to reduce Scope 1 and 2 greenhouse gas emissions by 35% and to reduce direct carbon dioxide emissions by 30%, both per metric ton of production. Clariant is well on track to reach these targets. Read more in Progress toward environmental targets 2025
In 2019, direct CO2 emissions (Scope 1) per ton of production decreased by 9.2% and greenhouse gas emissions (Scope 1 & 2) were reduced by 7.9%. This was mainly driven by changes in site ownership, an overall reduced energy consumption, as well as a shift away from heating oil to natural gas and purchase of green electricity at certain sites.
Since 2018, Clariant improved the comprehensiveness, transparency, and robustness of its greenhouse gas emissions data by reporting on emissions occurring along Clariant’s value chain (Scope 3 emissions). The reporting includes relevant activities such as the purchase of raw materials, energy-related emissions, transportation and distribution of supplied materials and sold products, and the end-of-life treatment of sold products.
The decrease of Scope 3 emissions between 2018 and 2019 by 12.3% was primarily driven by a decrease of CO2 in purchased goods and services, and end-of-life treatment of sold products. A detailed breakdown of Clariant’s greenhouse gas emissions is available in the GRI Report.
|
Continuing |
Discontinued |
Total 20192 |
2018 |
Change |
|||||||||
---|---|---|---|---|---|---|---|---|---|---|---|---|---|---|
|
||||||||||||||
Total greenhouse gas emissions (Scope 1 & 2 CO2 equivalents) (in m t) |
0.68 |
0.16 |
0.84 |
0.93 |
–9.7 |
|||||||||
Total indirect greenhouse gas emissions (Scope 3 CO2 equivalents) (in m t) |
|
|
4.99 |
5.69 |
–12.3 |
|||||||||
Greenhouse gas emissions (Scope 1 & 2 CO2 equivalents) (in kg/t production) |
171 |
609 |
198 |
215 |
–7.9 |
In 2019, Clariant continued rolling out its energy efficiency program eWatch™ to China. In addition, it advanced the digitalization of the program by piloting different business intelligence systems for energy management and by introducing smart metering to measure energy consumption. Clariant also introduced a monthly reporting cycle that includes Energy Performance Indicators on the site and country level. This allows Clariant to process and use energy data to improve energy savings and emissions reductions while increasing transparency. Furthermore, several sites were brought into compliance with the new ISO 50001 (2018) standard for energy management. At the end of 2019, 39% of Clariant’s sites were covered by ISO 50001.
Fear no colors
Light, tough, water-resistant and fast-drying – when it comes to sportswear and outdoor gear, synthetic fabrics are hard to beat. If taken good care of, these materials can last a lifetime, which makes their use very sustainable. Clariant and the Swedish start-up We aRe SpinDye® have teamed up to make them even more so. Together they have developed a method of spin-dyeing polyester. It involves coloring the fibers themselves before spinning them into yarn and weaving that into a fabric. That may sound obvious and has in fact been standard practice in many industries for decades. But it is only now catching on in fashion. Here, fabrics are usually dyed after they are woven, all too often using methods that use large amounts of water, harmful chemicals, and cheap labor in countries where wastewater management is lacking. Naturally, Clariant’s Business Unit Masterbatches knows a thing or two about coloring synthetic polymers. It supplies a host of industries with color-giving pellets called masterbatches, which are to be melted into clear plastics. Together, Clariant and We aRe SpinDye® apply that method to spin-dyeing polyester fibers in a large choice of colors. And they have already made a splash by teaming up with high-profile brands such as Quiksilver and Fjällräven. The hope is to make spin-dyeing the new industry standard for polyester fibers. According to We aRe SpinDye®, compared to piece-dye-finished fabrics, the process uses 75% less water, 90% less chemicals, up to 40% less energy, and reduces the CO2 footprint by about 30%.
Clariant made further progress in substituting fossil fuels with renewable energy sources. In 2019, the Knapsack, Germany, site joined the sites in Sweden and Belgium in making the switch to 100% renewable electricity. In addition, the sites in Tarragona, Spain, Bonthapally, India, Santa Clara and Coatzacoalcos, Mexico, increased their share of renewable electricity consumption.
In 2019, Clariant also worked to reduce Scope 3 emissions with several approaches, which included establishing a partnership with Neste to replace fossil-based feedstock chemicals with low-carbon solutions and moving strategic production sites closer to customers, thereby reducing transportation distances.
GRI Online Report
Management Approach Climate Change Material Topics – Advance
Idea to Market
1.4. Circular economy
Society, governments, and businesses are coming to the consensus that the circular economy is a viable alternative to the current linear way of conducting business. In a circular economy, materials are durable and reparable, kept in use for as long as possible, and are fully recovered or recycled at a product’s end-of-life. Ideally, material components are also renewable and sourced sustainably.
1.4.1. Target-oriented initiatives
Besides a continuous stream of policies and studies promoting the circular economy, Clariant observed an increasing number of brand owners promoting plastics recycling and registered more customer requests for collaboration in 2019. As a supplier to various industries, Clariant has the desire and vast potential to contribute toward achieving a circular economy. As a specialty chemical company strongly embedded in the plastics value chain, Clariant’s understanding of product-related recycling and deep chemical knowledge are clear advantages for developing circular solutions.
»We made ›Symphony of Collaboration‹ our theme for 2019 because it’s vitally important for the whole value chain to address the plastic waste challenge, and collaboration is the best way forward.«
Hans Bohnen Chief Operating Officer (COO), Member of the Executive Committee
In 2019, Clariant bundled its efforts to promote a circular and sustainable plastics economy under the motto »Symphony of Collaboration,« underlining the importance of the complete value chain in addressing the plastic waste challenge. As part of this effort, Clariant launched EcoCircle , a company-wide initiative to support the transition from a one-way plastics value chain to a circular plastics economy. With EcoCircle, Clariant extends its focus from the product to the entire value chain, identifying sustainable and viable solutions for a circular plastics economy. Clariant is also introducing worldwide EcoCircle Centers of Excellence dedicated to collaborative research and joint development of products and solutions for a circular plastics economy. Specialized teams and facilities will allow Clariant to channel expertise and develop specialty products for specific circular applications. Read more in Circular Economy
In 2019, Clariant introduced four sustainability designators that enable customers to identify products with key advantages. The »Circle« designator highlights products that contribute to plastic recycling and the circular economy. Read more in Launch of four sustainability designators
Launch of four sustainability designators
In 2019, Clariant introduced four so-called sustainability designators to help customers looking for particular sustainability attributes. The four suffixes are applied to the end of product names to identify products with key advantages in certain areas:
Aqua – water saving
Found on products and solutions that support customers and the value chain in saving at least 20% of water in the direct or end use of their products.
Terra – renewable feedstock
Found on products and solutions containing a significant share of renewable resources with mass-balance certification or real renewable content reaching a Renewable Carbon Index of at least 50%.
Circle – circular plastics economy
Found on products with the primary purpose of supporting the reduction, reuse, or recycling of plastic products demonstrating a beneficial and validated performance.
Vita – natural ingredients
Found on products and solutions that contain enough natural und renewable ingredients to achieve at least 98% on the Renewable Carbon Index.
1.4.2. Tangible results
Clariant was awarded the Material Health Certificate GOLD level certification from the Cradle-to-Cradle™ Products Innovation Institute for Licocare® RBW Vita, a renewable and competitive processing aid for formulators of bioplastic compounds. The Material Health Certificate uses the rigorous, globally recognized material health assessment methodology of the Cradle-to-Cradle Certified™ Product Standard to verify a product’s support for safe and circular products. All ingredients present at concentrations above 100 ppm in a product are assessed. The certificate is highly valued among brand owners and facilitates customers’ ambitions to certify their final products. In order to receive the Cradle-to-Cradle™ certification, Clariant collaborated closely with the Swiss-based certifier, the Environmental Protection Encouragement Agency (EPEA).
Cradle-to-Cradle™
The Cradle-to-Cradle™ certification assesses a product along five dimensions: material health, material reutilization, renewable energy and carbon management, water stewardship, and social fairness.
1.4.3. Advancing together
For the circular economy to take off, innovation and collaboration are paramount. To strengthen its impact and deliver its sustainability ambition with other like-minded companies, Clariant joined the World Business Council on Sustainable Development (WBCSD) in 2019. Clariant is contributing to the WBCSD Circular Economy Initiative Factor 10, a project that brings companies together to rethink the current way of finding, using, and disposing of the materials that make up global trade, and aims to create scalable solutions for businesses. Clariant also contributed to the WBCSD’s CEO guide to the Circular Bioeconomy, which calls for a shift toward a sustainable, low-carbon, circular bioeconomy and provides a clear view on the concomitant economic opportunities.
Together with 29 multinational companies that use, sell, process, and recycle plastics, Clariant founded the Alliance to End Plastic Waste (AEPW), which was launched in early 2019. The AEPW’s mission is to end plastic waste in the environment by cleaning up rivers that carry vast amounts of plastic waste to the ocean, building infrastructure to collect, manage, and recycle waste, advancing and scaling new technologies, and educating and engaging governments, businesses, and communities to mobilize action.
GRI Online Report
Management Approach Circular Economy Material Topics – Focus
These are plastic additives in the form of granules with dyestuffs or other additives used to dye or alter the properties of natural plastic. View entire glossary
Pigments are substances used for coloring; they are used in a technical manner, for example in the manufacture of dyes, varnishes, and plastics. View entire glossary
Stakeholders are people or groups whose interests are linked in various ways with those of a company. They include shareholders, business partners, employees, neighbors, and the community. View entire glossary
A substance that lowers the activation energy, thereby increasing the rate of a chemical reaction without being consumed by the reaction itself. View entire glossary
The value chain describes the series of steps in the production process, from raw materials through the various intermediate stages to the finished end product. View entire glossary
Compliance is a key element of Corporate Governance. It refers to compliance with the law and directives as well as with voluntary codes within the company. View entire glossary
The value chain describes the series of steps in the production process, from raw materials through the various intermediate stages to the finished end product. View entire glossary