»No more guesswork«
Contribution to SDGs
This story is an example of Clariant’s contribution to SDG 9 and SDG 12. Read more in Sustainable Development Goals
-
Build resilient infrastructure, promote inclusive and sustainable industrialization and foster innovation
-
Ensure sustainable consumption and production patterns
Artur Kulawiński, Market and Risk Manager at Clariant, talks about the company’s holistic approach to digital risk management along the entire supply chain.
Artur, Clariant won two awards in 2019 for its procurement. What is it you’re doing so well?
Both those awards essentially recognize the way we look at sustainability and risk along our entire supply chain – what we call modern holistic risk management.
Why is there a need for that?
Supply chain risk management has never been more important. That is especially true for the chemical industry. Ever tighter regulation and increasing awareness of sustainability are reshaping our industry. Managing the risks that can jeopardize compliance with these requirements throughout a global supply chain is hard. But it is vital to our business. So Clariant established a system that looks at risks across all Business Units, involves everyone in procurement, gives deeper and more useful insights, and leverages all the best digital tools available today.
What makes Clariant’s risk management »holistic«?
The new emphasis on supply chain risk was initially driven by our efforts towards sustainability. But we decided to actually take a broader view. Our system very methodically monitors all the different kinds of risks. Plus, it not only aggregates information in real time but also actively works to eliminate or mitigate those risks together with our Business Units.

Artur Kulawiński
Market and Risk Manager
POLAND
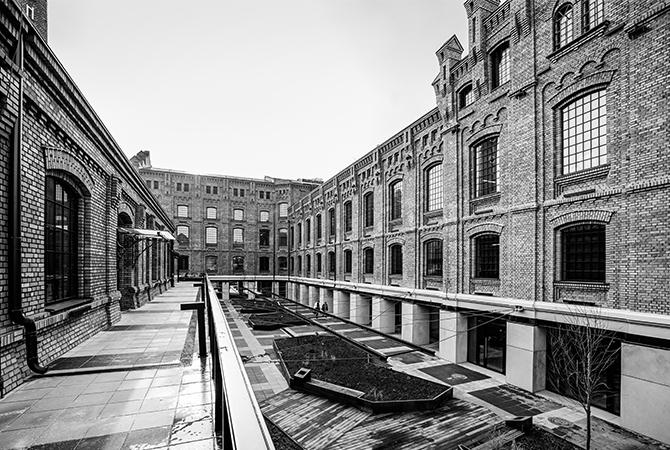
New premises
The new headquarters for Clariant’s Global Business Service in Lodz, Poland
What are some of those risks?
First, there are production and supply risks, anything and everything that can disrupt our ability to deliver products. That can be natural disasters, strikes, or accidents – either at a plant or in transport. Then, there are environmental risks. Those are issues our suppliers may have in terms of environmental protection at their sites, for example. That can be a question of where their sites are located, but also of how committed they are to environmental safety and protection. There are also financial risks that can arise from bankruptcy or just generally poor financial health of a supplier. And finally, there are reputational risks, if any of our suppliers were accused of, say, bribery or child labor. That risk has increased significantly with the advent of social media.
Are all of Clariant’s Business Units equally affected by those risks?
That depends on the materials and the markets they deal with. Some face more environmental, others more financial risks. Some industries are prone to force majeure incidents like natural disasters simply because of where their raw materials come from. And some, such as our Business Unit Industrial & Consumer Specialties, are particularly close to consumer brands, which are very sensitive to reputational risks.
What role does regulation play?
We are a chemical company, and we work with a wide range of highly regulated industries, including food, automotive, cosmetics, pharmaceuticals, consumer goods, and agriculture. So we need to be compliant with hundreds of thousands of regulations, which are also constantly evolving. Every quarter sees a significant increase and tightening in regulations.
How has that impacted Clariant in the past?
In China, for example, we’ve lost suppliers literally overnight. I remember a case where a plant was closed because, according to new regulations, the site was now too close to a river. We were basically informed that our supplier didn’t exist anymore – or would at least need a couple of years to relocate production.
Awards in 2019
Acclaimed procurement
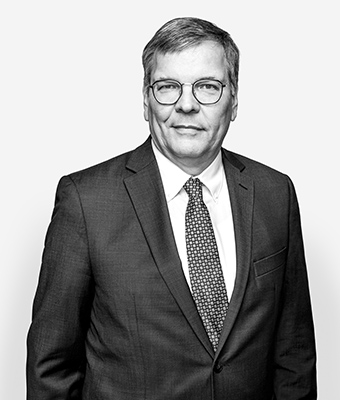
Markus Mirgeler
Head of Group Procurement Services
In 2019, Clariant earned two awards for its novel approach to supply chain risk management. The first was the EcoVadis sustainable procurement leadership award for having the »Best Internal Stakeholders Engagement.« The second was the World Procurement Award 2019 in the »Supplier Risk Management« category. In both cases, the awarding organizations highlighted Clariant’s efforts to go beyond its procurement team and instead involve multiple internal and external stakeholders for a more integrated supply chain process. »Integrating sustainability and risk management along our supply chains is a cross-departmental responsibility and requires a broad commitment in order to be a success,« says Markus Mirgeler, Head of Clariant’s Group Procurement Services. »So we are very proud of getting this great recognition and see it as an inspiration to keep pushing ourselves.«
How did you respond?
In that case, Clariant had to discontinue the product in question. The material we needed involved protected intellectual property, and there was no alternative and no other source to turn to. That shows how immediate and far-reaching the impact can be. And this kind of thing has happened more than once.
Is that a problem specific to China?
No. The regulatory environment is different everywhere. But each country has its own risks. We have long-standing relationships with suppliers in Germany, for example. That can backfire just as well. When you’re relying on a supplier via pipeline, all it takes is one small incident for production to grind to a halt. Or think of the Rhine. Droughts and low water levels have in the past made parts of it unnavigable for weeks at a time, crippling parts of the chemical industry concentrated along its banks because they rely on it for cooling and transportation.
Single sourcing is an obvious risk. Is Clariant working on that?
Absolutely. And not just for risk mitigation. It’s also hard to cut costs and increase competitiveness when you are locked in like that. So we work to combat single sourcing, most importantly by helping and challenging our Business Units to find alternatives. But that is a long-term process. It can take up to two years to qualify an alternative. And sometimes there simply isn’t one. Then, all you can do is build a stock and prepare to react to any disruption as fast as possible.
How does speed help?
If we are the first to know about a potential disruption, we might be able to very quickly acquire any available stock before it runs out or the price goes up.
Has that happened?
Yes. Not too long ago, we had a case where a procurement manager received an alert about a fire at a facility of one of our suppliers. He wasn’t able to contact his key account manager, so he took mitigating measures into his own hands and acquired a safety stock just before the price jumped by more than 20%.
How do you prepare for these kinds of events?
That is where our holistic approach comes in. Identifying risks is one thing. Managing them is another. We prepare for specific scenarios by establishing action plans together with our procurement managers.
What helps you predict risks?
The traditional and most thorough way to know your vendors is to audit them. And that is something we do. But with about 66 000 listed suppliers, there is no way of covering them all. And an audit only gives you a snapshot anyway. It doesn’t tell you much about what might happen next week or next month. That’s why we rely on digital technology and artificial intelligence, AI, to gather a lot more information in real time. We use a digital tool that lets us monitor more than 300 000 online sources – anything from news outlets and social media channels, to insurers and credit information providers, to government agencies and NGOs.
How does artificial intelligence help?
The tool uses about 100 indicators to screen those 300 000 sources for information on around 8 000 of our direct, indirect, and logistics vendors. Without the use of AI, there is simply no way of cutting through the noise and filtering relevant information. AI also helps eliminate trolls and misinformation. That way, we get relevant alerts in real time about any event that may impact our supply chain, and I make sure that information – along with a link to the source – reaches the right person to create an action plan.
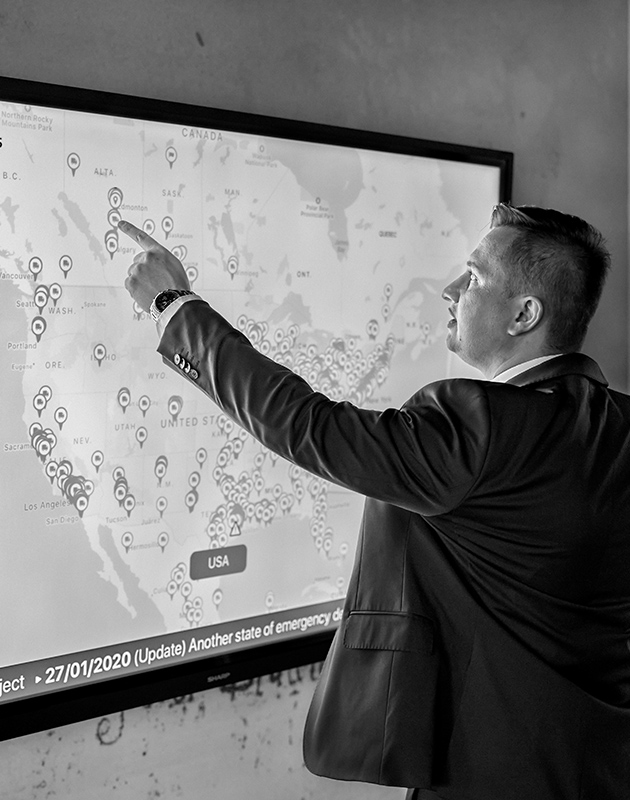
Instant alerts
Artur Kulawiński is able to monitor thousands of suppliers across the globe.»Mitigating the impact of a single major event easily covers the cost of the entire program for a year.«
What other tools are you using?
At the most basic level, we’ve established a process of self-assessment for our vendors with the help of Integrity Next. This service allowed us to check more than 12 000 of our medium- and low-spend vendors within the first few weeks. We found that 6% of those required further auditing, and we’re currently extending this check to all our suppliers where assessment is needed.
What about those vendors that are especially critical to Clariant’s business?
For our most critical vendors, we have a complete system in place that provides an individual risk scorecard. We aggregate all the information we can gather from our digital tools, from external evaluations by tools such as EcoVadis and the Together for Sustainability initiative, as well as from our own audits. We add the input of anyone at Clariant who’s ever dealt with the company subject to the assessment. That gives us about 100 different risk indicators and an aggregated risk score for each of those critical vendors.
Who works with that information?
We have about 200 active users. As a kind of gate-keeper, I manage the database and ensure that all collected information and the scorecards are made available to anyone within procurement. For the most part, it’s procurement managers, tactical buyers, regional heads, and category managers who use the information on a regular basis.
What does that risk score look like?
We boil it all down to a score between 0 and 100, where 100 represents a disrupting event happening right now. The score is updated in real time. So while a disruption brings up the score immediately, it will also revert back to its previous level as soon as we hear the issue has been dealt with adequately.
What’s the average score?
The average score is in the mid-50s. Anything below 40 is considered good or very good. The best scores are in the low 20s. But there is no business without risk, so there is no supplier scoring anywhere near zero.
How does this holistic risk management affect Clariant’s bottom line?
That is not easy to measure. We obviously can’t tally a number of yearly disruptions to avoid. But we confidently estimate that every dollar spent on prevention or mitigation will save roughly five dollars in damage. Or look at it this way: A single major event, like the one we had with the fire, easily covers the cost of the entire program for a year.
What are your goals?
There is always room for improvement. For example, by fine-tuning what we monitor, what is relevant, and to whom. We’re working to cover even more of our spend and to identify further critical suppliers. Another aim is to bring down the average risk score to around 35 – 40 by the year 2022 and to significantly decrease our rate of single sourcing. In a way, that is the real beauty of the system: having those numbers to work with. Risk has always been something you had to take into account in procurement. What we’ve done is take out a lot of the guesswork. We’re relying on data rather than a gut feeling.
Compliance is a key element of Corporate Governance. It refers to compliance with the law and directives as well as with voluntary codes within the company. View entire glossary
Stakeholders are people or groups whose interests are linked in various ways with those of a company. They include shareholders, business partners, employees, neighbors, and the community. View entire glossary