Working with the sun
Treating the earth responsibly when removing its valuable minerals: this is a vision of sustainability that generates enthusiasm even in the driest corner of Sardinia. There, a bentonite mine presents the best example of open-pit mining carried out in an environmentally compatible manner.
PHOTOGRAPHY Jo Röttger
TEXT Bertram Job
The main island of Sardinia is divided into about 20 topographical areas, and if it were up to the 2.5 million tourists a year, La Nurra would be at the bottom of the popularity scale. On the other side of the sheer, hard-to-reach cliffs, the dry plateau in the northwest area of the second largest Mediterranean island appears to offer only bushes, dust, and persistent winds for the most part. More than fifty years after malaria was eradicated here, proper villages, let alone noteworthy towns, can hardly be found to this day. On average, there are five people per square kilometer. For geologists and mineralogists, however, the region ranks near the top. Layers of earth from the early Tertiary period, which are of great interest, are hidden in its limestone and shale. There is evidence that silver was mined at Capo dell’Argentiera since Roman times up until 1963. And further inland, at s’Aliderru, crawlers and excavators bring a special treasure to light each day: white bentonite, a clay buried up to 40 meters below the earth’s surface, and formed between other geological layers over many millions of years. Its impressive absorbent and binding properties are primarily due to the layered minerals of the bentonite, which has been formed from compressed ash under high pressure for millennia.
Worldwide, there are 57 different types of the precious clay, which is further processed in very different industries – for purification of edible oils and fuels, as an additive for pharmaceuticals, in papermaking, for drilling, etc. For calcium bentonite, which is mainly used in foundries and the pelletization of steel, this area is reputed to be one of the best, even far outside of the region. Francesco Loi explains this sooner or later to every visitor onsite. »This is the backbone of our opportunities in Europe,« he says in a penetrating, bassy voice with unmistakable pride.
With this, he is referring to the Società Sarda di Bentonite (SSB), which manages the operation, and for which Loi, a man in his fifties with jet-black hair, works as Operation Sites Manager. He is also referring to the Clariant Group, which, as the owner, strives for the long-term use of the deposit – an ambitious strategy that is not limited to exploiting the resources. This is also clearly spelled out in the guidelines (»Our Mission«) of the Functional Minerals Business Unit, which state, »We create value through sustainability and innovation.«
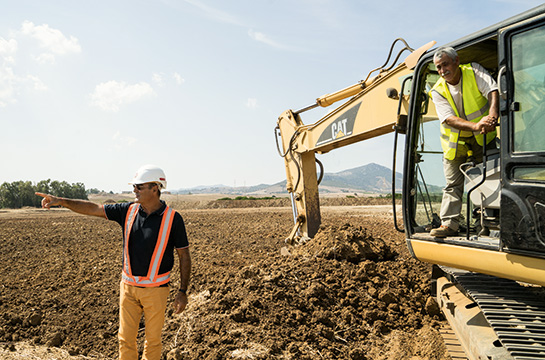
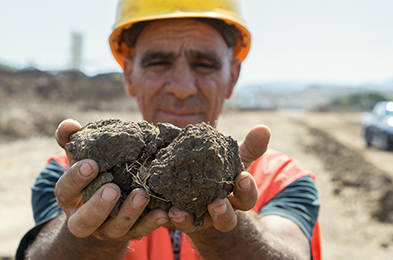
These are guidelines that Loi and his team are only too happy to comply with and improve on. Every February, after the rainy season, they resume excavating the precious clay from the expansive, sprawling open pit. Tractor-trailers take the clay to the adjacent factory load by load until November. The factory is an open station comprising silos, office containers and a well-equipped laboratory in which Alessandro, the chemist, analyzes samples of the excavated material for all relevant parameters on a daily basis.
Loi explains that for a long time, his people were largely limited to pressing a few buttons in the silo factory. That was enough to activate the bentonite with sodium carbonate and to prepare it for further processing in Santa Giusta – the main plant in the port of Oristano, where it is dried and shipped to Europe. However, this also meant hauling the raw material, which still contains around 40% water, a distance of 160 kilometers – and using a lot of oil and energy at the destination to further reduce the water content to around 12%, the level required for further transport. This entailed a great deal of emissions, from the truck to the rotating dryer.
Since that time, however, the site manager and his engineers have been able to significantly improve the process. Now, as Loi notes, they are all much busier outside, because clay of various colors is now spread out ankle-deep around the plant. With this, one can easily guess what is taking place here. Resources are being conserved by using solar energy to dry the bentonite. In this manner, the rock is sent to Santa Giusta with a significantly lower percentage of liquid, where it can then be dried faster.
Ultimately, this saves some tons of weight per truck and reduces the transport costs significantly. This means less strain on the environment, lower costs for the company – and noticeably greater efficiency. »We are now able to produce more material in less time,« Loi sums up. This is a significant advantage in international competition, in which a great deal revolves around the predictive calculation of demand.
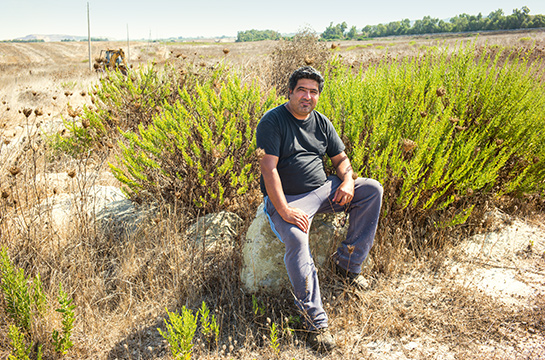
This progress is entirely to the liking of the native islander, who is a dyed-in-the-wool patriot like many others here. It does not take long to realize that these plots of earth are the greatest thing of all to him – and thus also the most worthy of protecting. In addition, this technological breakthrough goes hand in hand with the thriving Clariant Business Unit’s philosophy, which always strives for both long-term access to minerals through sustainable development and a leading role in the global market. This aspiration is underscored by 39 mines on three continents and 1.9 million tons of bentonite production per year for customers in some 130 countries.
The company has provided substantial funding for the restructuring of the drying process. To acquire land for drying in the sun, an additional 18 hectares of land were leased in s’Aliderru. Clariant guaranteed the municipalities that the land would be returned unharmed at a later point. Moreover, another mine further north was closed. Additional clay can now be dried in this area. Contractors use a respectful approach to soil management. Each cubic meter of excavated soil is expected to be backfilled exactly where it was taken from after the mining. And the surface is subsequently recultivated at the company’s expense and returned to the farmers for ongoing agricultural use.
FRANCESCO LOIOperation Sites Manager, BU Functional Minerals»We should not leave any footprint on the land, because it is not ours. We must eventually return it to our children.«
Under these circumstances, Francesco Loi sometimes has the air of a conductor. He must set the tempo, open up the soil, temporarily store large amounts of earth, and then fill them back in at the appropriate time. The landowners, including many small farmers, benefit from the lease. It ensures their existence. And for Loi himself, there is no alternative to this use of resources. »We should not leave any footprint on the land, because it is not ours. Everything is merely borrowed. We must eventually return it to our children.«
What has been started with this apparently has not yet reached any endpoint. Loi and his staff have long kept some of the surfaces of the mine open for experiments. There, they attempt to dry the bentonite even further with the help of the sun before it is brought to Santa Giusta. This is a real challenge, with the last percentage of water being particularly difficult to get out of the clay. By this point, the clay has been laid out up to seven times, which takes a few weeks.
But isn’t tenacity a quality that people on this island want more than any other? »We believe in our idea,« says Loi. This was the case a few years ago when their idea was first developed in an exchange among engineers and decision-makers distributed throughout Sardinia, Switzerland and Bavaria. »And now we are implementing it step by step.«